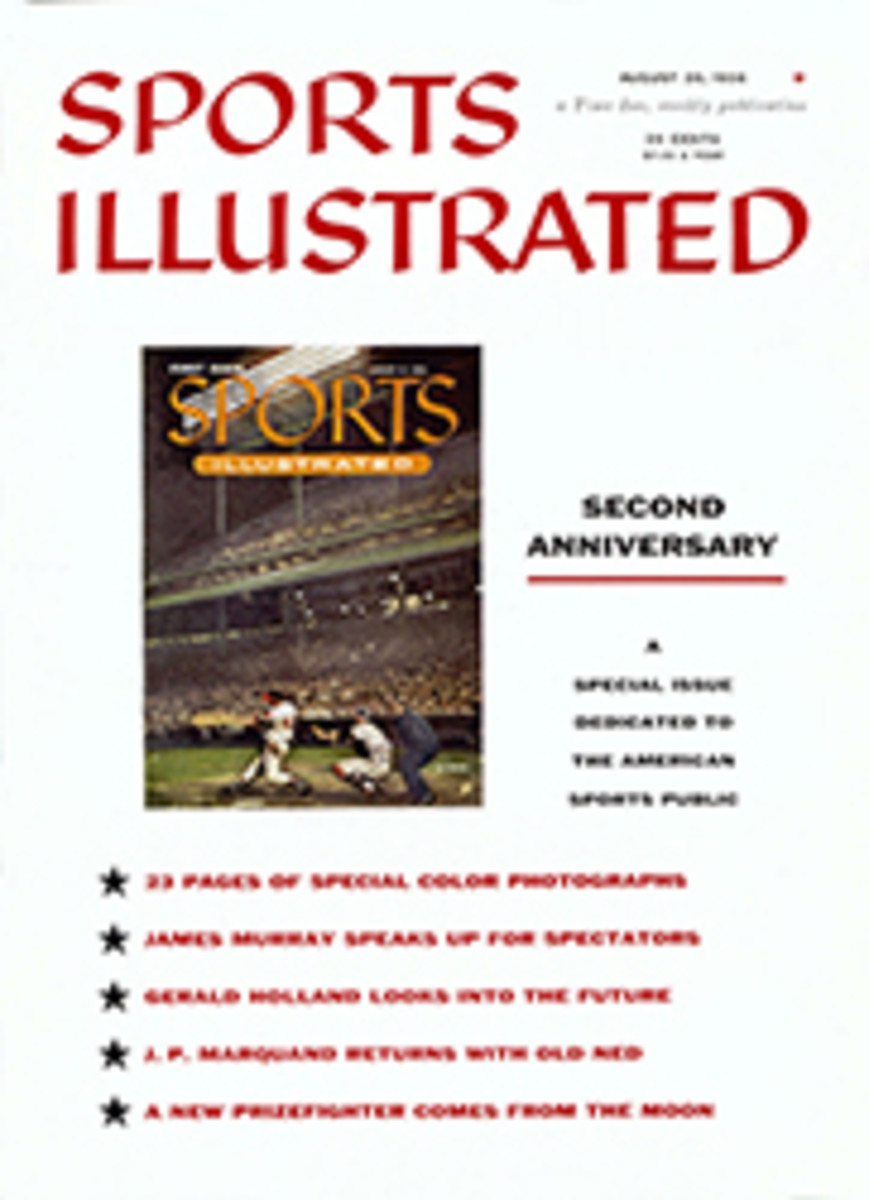
BOATING TODAY AND TOMORROW
In the composite drawing above, SPORTS ILLUSTRATED is looking at the boat of the future. The boat itself is a Bell Boy plastic runabout, convertible into a fishing craft or family cruiser. The metal vanes are hydrofoils, made by Atlantic Hydrofin Corp., which hike the hull out of the water, increasing its speed by 50%. The engine is a futuristic water jet outboard. Turn page for more on plastic boats and drawings of the outboards of the future
BUILDING BOOM FOR FIBER GLASS
The brightly colored boats at right and on the following pages are doing more to change the yacht-building industry than anything since the introduction of the gasoline engine. Every one of the models shown—each selected as representative of the types that have taken over 15% of the U.S. boating market in 10 short years—is made of fiber glass-reinforced plastic, probably the most promising material ever conceived for the building of small boats.
The basic components are fiber glass cloth, or matting, and a gooey plastic called polyester resin which, when combined, will harden into a compound that is lighter than aluminum, tougher than steel and easy for a skilled worker to set into a mold of almost any imaginable shape. Hull curves like those on the Lone Star Meteor (see page 67), which would have been difficult if not impossible with wood, can be turned out in fiber glass plastic in a matter of minutes. Hull strength is barely believable. A small plastic wherry the Bellingham Shipyards Co. left in the water all winter, banging against tidal rocks, was pulled out whole and sound in the spring. Besides these impressive virtues, a boat made from fiber glass and polyester will not do any of the following things that all steel or wooden boats must do eventually: rot, corrode, rust, dry out, give way to marine borers like teredos, absorb any amount of water, or just generally get old from exposure to weather. Furthermore, unlike a wooden boat, a fiber glass plastic boat need not be soaked every spring until the seams close. Nor need it be caulked or extensively painted.
Polyester, which was born out of World War II as a shatter-proof liner for self-sealing airplane gas tanks, made its yachting debut in 1946. That year the Winner Manufacturing Company of West Trenton, N.J. introduced the first plastic boat ever shown at the New York Boat Show, a 10-foot dinghy made from polyester reinforced by sisal fibers. It was not terribly successful. After a few months in the water the sisal, even though surrounded by protective resin, absorbed enough moisture to start a vegetable rot. Besides, people were used to wooden boats and plastic revolted their sense of tradition.
Then two research developments sent the industry on its way. Owens-Corning Fiberglas Corporation marketed the first fiber glass matting, a rot-proof pad of random fibers which provided the structural thickness Winner had tried to get from sisal. At the same time Pittsburgh Plate Glass came out with a polyester that set at room temperatures under atmospheric pressure, thus doing away with the expensive metal molds the early experimental boats had required.
With these ingredients in hand almost anybody could make a plastic boat, and almost everybody did. Hundreds of one-man companies popped up around the country, making molded boats out of matting, or covering wooden boats with a layer or two of cloth. A lot of the boats they turned out were incredibly bad. Some of them were so poorly designed and had so little glass reinforcing that the hull flexed in and out like the sides of a cracker tin. Some builders tried to strengthen their hulls by extra laminations, but laminated one weak spot right on top of another. Others built boats with inadequate flotation compartments. Fiber glass plastic has a density of 1.65, and a swamped boat sinks like a rock unless it has plenty of styrofoam or wood built into it.
None of this did anything to promote fiber glass. Nor did the trumpetings of overenthusiastic promoters who claimed their material would not burn (it will), needed no paint (impregnated colors fade in the sun and all boats can use a good coat of anti-fouling paint to keep off the barnacles), or that any amateur could make a boat from it (an all-plastic hull is a job for real professionals). That was the situation as late as 1950, when the total U.S. market was less than 5,000 boats and only the five biggest companies turned out more than 200 boats apiece.
Gradually, however, the inherent excellence of the product provided its own leverage to force the market. In 1953, 8,000 solid plastic hulls were sold, with enough additional cloth and plastic for do-it-your-selfers to cover twice that many wooden boats. The substandard builders slowly began to die off, and the reputable ones learned to dress up their boats with enough mahogany to satisfy the staunchest traditionalists.
In 1954 fiber glass arrived. Sixteen thousand boats were built and bought. In 1955, 30,000 boats. By December of this year, 12 months' sales will have reached 40,000, with an additional existing total of 200,000 wooden boats with fiber glass skins.
A typical example of the booming young builders is the Bell Boy division of Bellingham Shipyards. Three years ago Bellingham wasn't even in the fiber glass boat business. Last winter at the Seattle Boat Show their Bell Boy boats set a sales record of $250,000 off the floor, the company's entire productive capacity until May for all nine of their models. The other leading concerns like Glasspar (tops in the nation with over 3,000 hulls per year), Wizard (2,000), Lone Star, Winner and Crosby Aero-Marine are experiencing the same exciting growth.
So far, structural problems and a tendency of polyester to fatigue at points of stress have limited mass production to craft of about 24 feet and under. But bigger vessels like the 42-foot ketch Arpege or the Platzer Boat Co.'s 65-foot twin diesel cruiser are being built, and some grandiose plans are in the works. An official from the Navy's Bureau of Ships has said that the department is ready to spend up to $14 million on plastic boats in an effort to cut the $15 million lost each year on rot and corrosion in wood and steel boats. And last month in Los Angeles, Zenith Plastics Co. launched the first of a fleet of 25 36-foot plastic landing craft for the Navy. The Coast Guard is currently testing three plastic versions of its 40-foot patrol boat.
In the civilian market, with a good slice of the motor-boat field already in hand, the plastics people are moving into sailboats. Classes like the Rebel, built exclusively of fiber glass plastic, have reached the seven hundreds after only three years of production; and many older classes—Comets, Snipes, Moths, Ravens—have authorized its use in standard or experimental models. This spring even the dignified old Atlantic Class, long closed to anything but its existing 100 wooden boats built 27 years ago in Germany, threw itself open to fiber glass.
With advancing research and the gradual elimination of substandard builders, the future of the fiber glass boat appears unlimited. It would be ridiculous to say that some day all small craft will be made from fiber glass, but it is perfectly accurate to say, as Winner's President I.M. Scott did not long ago: "Here's a material that's perfect for boats. As a matter of fact, I'd say that fiber glass is better for boats than it is for anything else; and it's better for boats than any other material."
OUTBOARDS OF THE FUTURE
In the middle of the nation's biggest, busiest outboard season, with manufacturers racing to meet public demand for more and faster engines, SPORTS ILLUSTRATED asked Brooks Stevens, noted designer and architect of the-popular Evinrude Lark and Johnson Javelin, to take an authoritative look into the outboarding future. Stevens' designs of tomorrow, shown for the first time on these pages, reveal some startling possibilities, a few of them perhaps 40 or 50 years from realization,, many less than 10 years away. Turn the page for more future outboards.
Production of the Brooks Stevens ideas and those on the opposite page done by Designer Charles Clarke for Scott-Atwater will be delayed until manufacturing costs of heat-resistant high-alloy steel can be brought down. Other complex problems, such as scaling down the hefty gas turbines of today, must be solved, and the consumer market has to be prepared for the radical change from present designs. Within these limits, however, even the 100-mph racing jet below and the sun-powered unit opposite may appear on the outboard boats of tomorrow.
WATER JET
Reciprocating engines in streamlined housings on either side of motor head drive pumps that suck water through intake slots at front of vertical stems, then discharge it at high speed through underwater jet nozzles. Pressure-operated speed indicator is mounted on top of the motor above control levers.
TURBOPROP
Gas turbine similar to jet plane motor drives twin propellers that allow boat to be maneuvered like two-engined inboard cruiser. Air drawn in through slots around speed indicator mixes with gas vapor. Mixture explodes and thrusts against metal vanes which turn drive shaft. Exhaust gives added push.
TURBOJET
Double turbines throw exhaust gases to rear, forcing engine ahead at possible speeds of 100 mph or better. Boat is steered by twin rudders fashioned in shape of inverted V to function effectively on banked turns. Adjustable horizontal plate above the rudder counteracts tendency of a fast moving hull to take off from the surface of the water.
WHEEL STEERING
This will probably be first of future outboards to appear on the market, is designed to push heavy-duty work boats with five-cylinder, 50-hp radial engine. Rugged auto-type steering wheel turns lower unit without affecting stationary head. Counter-rotating propellers eliminate torque common to present-day single-prop motors.
UNDERWATER COOLING
Engine for turboprop is encased in underwater tube, simplifying problem of cooling hot gasoline turbine. Position of motor keeps center of gravity low, acts as stabilizing factor for small boats. Engineers have already built experimental turboprop for Soott-Atwater, but refinements and retooling may delay production 10 to 20 years.
SUN POWERING
Solar battery that gets power from sun's rays concentrated in polished reflector mounted on top of the engine is most radical of futuristic ideas. Battery drives noiseless electric motor housed below the waterline between counter-rotating propellers. Capacity of battery is sufficient to keep the engine running on cloudy or rainy days.
ILLUSTRATION
JAMES CARAWAY
PHOTO
FIBER GLASS REBEL is 16-foot racing sloop. Class, started in 1953, numbers more than 700 boats. Cost with sails is $1,500.
PHOTO
EXPRESS CRUISER made by Bell Boy division of Bellingham Shipyards, Washington, measures 18 feet, has head, sink and two bunks. Express takes inboard or outboard power. Outboard price without motor: $2,195. Inboard: $4,000 to $4,300 with motor.
PHOTO
BELL BOY BIKINI, shown below for the first time anywhere, will be marketed in November. Bikini, to cost between $5,000 and $8,000, was designed by Hydro Racer Ted Jones as a super family runabout that gives safe ride at speeds up to 100 mph.
PHOTO
GLASSPAR KAYAK carries two, measures 11 feet and is designed for either lake cruising or river running. Kayak costs $225.
PHOTO
BALBOA RUNABOUT by Glasspar, Santa Ana, Calif. is 13 feet long, holds four, takes 25-hp outboard. Cost: $435 with windshield.
PHOTO
VIKING RUNABOUT built by the Winner Mfg. Co., Trenton, N.J. carries price tag of $985 with windshield and wheel steering. Viking, 16 feet over all, is two feet longer than the average runabout, handles six passengers and takes outboard up to 50 hp.
PHOTO
AVALON CONVERTIBLE by Glasspar has removable canvas top. Boat measures 16 feet, holds up to five passengers. Cost: $1,115.
PHOTO
UTILITY RUNABOUT built by Wizard Boat Co., Costa Mesa, Calif., is 14 feet long, used mostly for fishing. Price is $415-460.
PHOTO
LONE STAR METEOR is most radical of current plastic boats, features auto-type headlights, twin tail fins in rear. Cost: $1,600.
SIX ILLUSTRATIONS