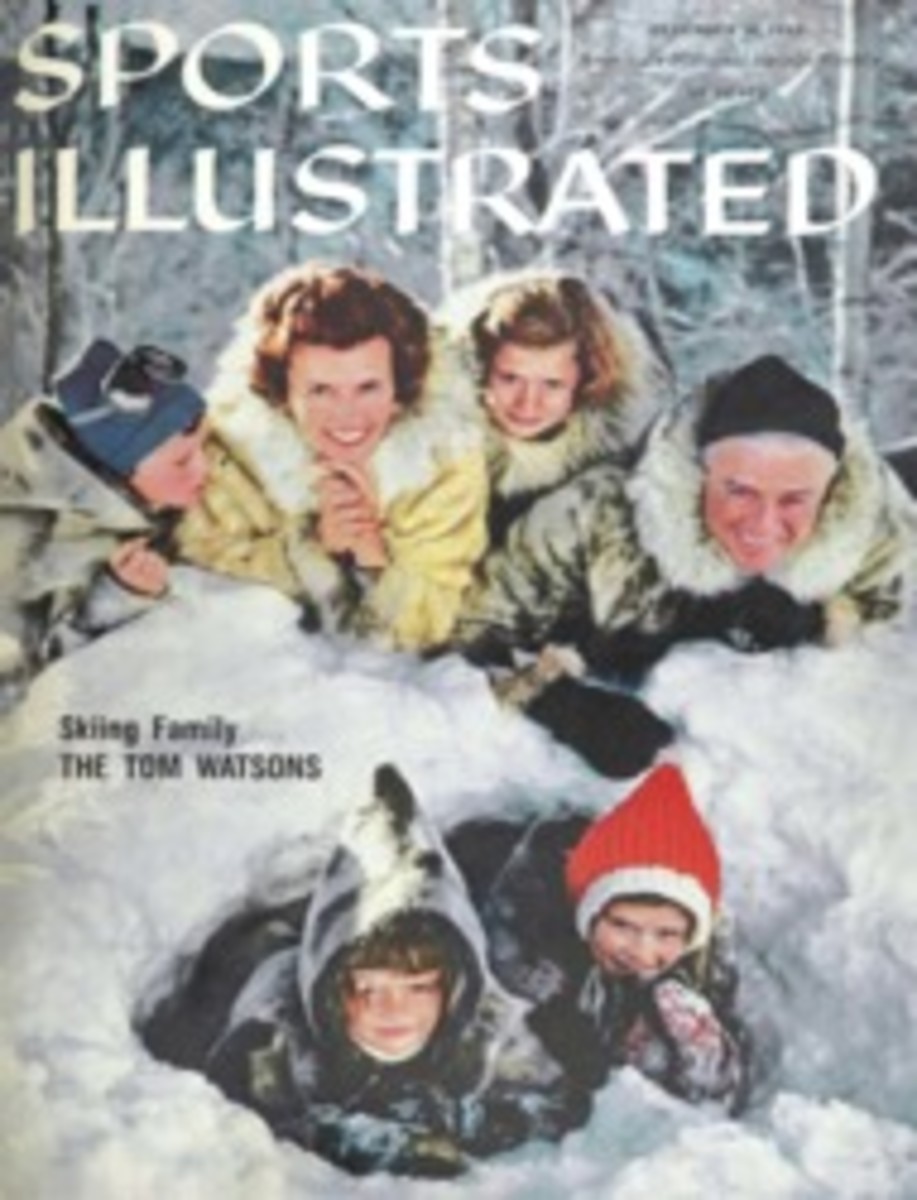
BY ARTISTRY OUT OF MASS PRODUCTION
BIRTH OF A BOAT
Shown here, ready for production, are men and materials to make a 33-foot Chris Craft sports fisherman. For the story of boat and builders, turn page
If boats had stud papers the way race horses do, the pedigree for the 33-foot deep-sea fishing boat shown at left would read, "By Artistry out of Mass Production." The particular artist in this case was A. W. (Bill) MacKerer, Chris-Craft's vice-president for manufacturing and engineering, and a marine architect of considerable skill. Three years ago MacKerer took a swing around the country and, in talks with dealers and anglers, sensed a need for a relatively inexpensive sport fisherman.
To design and build one would be no easy chore, for boats like this have always been the aristocrats of the motorboating world. The very best of them measure about 40 feet overall, big as powerboats go but barely big enough to carry the high-speed engines, huge cockpit, and endless paraphernalia of big-game fishing. For the most part, they have been custom-made or custom-altered by men to whom a mystical knowledge of fish and the sea has been attributed by their grateful customers. The high priest of the trade has, for the past decade, been John Rybovich (SI, Oct. 28, 1957) of West Palm Beach, Fla., who builds six masterpieces per year for something like $70,000 per copy. And hardly a stick on these 40-footers is not fashioned or fitted by hand.
That was the only way to make these boats until the Chris-Craft shown here was born. This little thoroughbred measures only 33 feet, yet she carries all the gear an angler needs, and can bang through a sea or battle a fish with the best of them. Furthermore, she is strictly a mass-production baby. Every four days, a vast but very well-ordered load of 26,851 screws, 2,425 board feet of mahogany and an infinite variety of metallic shapes (see pages 48-49) goes into one end of Chris-Craft's Pompano Beach, Fla. plant. Every four days a finished boat comes out the other end. The price of the bare boat: $19,840. Fully found, with all the optional extras such as electronic depth sounders, heavy-duty fighting chair and the canvas top, she costs $26,175—still not exactly a giveaway but nonetheless a good 60% below the price for her handmade predecessors.
The birth of the new boat actually began in late 1956 when MacKerer laid out the basic lines. He decided on a 33-foot length and a weight of six tons because it was "about as small a size as would perform well in heavy seas." His experience told him that a beam of 11 feet would keep the hull from burying. He drew in a sharp V shape in the entrance so the boat could enter heavy seas without pounding. He designed the galley and other components with mass production in mind, so they could be built independently. After he and Chief Engineer E. L. Eckfield determined the proper shaft angle and engine positions, the entire boat was laid out full-scale on a drawing board 80 feet long. Then the boys from purchasing and sales came in to approve the design.
FIRST O.K. FROM SALES
At Chris-Craft, this once-over by the top sales executives is no casual matter. Chris-Craft is the world's biggest producer of engine-powered pleasure craft. Last year at eight factories, scattered between the mother plant in Algonac, Mich, and the new headquarters at Pompano Beach, they turned out 8,000 boats in 42 different models. Total annual sales are around $40 million, and Board Chairman Harsen Smith was not about to rush out and lay an egg in the freewheeling traffic of today's boating market.
Therefore, the outlined image of the 33-footer got a close going-over before she was approved and the hull-framing date set. The production schedule ordered the first boat in the water 60 days after keel laying. Thereafter, a new boat was to appear every four days.
Meeting a demanding production schedule such as this one is not only a Chris-Craft specialty, it is almost the company's raison d'être. Since Chris-Craft first emerged from its humble beginnings 70 years ago as a duck-boat builder in Algonac, the compny has been strongly influenced by the assembly-line techniques of nearby Detroit. Since then, it has had its greatest success in production building of models that previously had been thought of as custom items. Today every one of its boats, from the 17-foot Sportsman at $3,335 up to the 66-foot Constellation motor yacht at $159,970, is turned out on a production line. The 33-footer is no exception.
Like all Chris-Crafts, she is cut out initially as a complete kit of numbered parts. An elaborate routing system then schedules each number to meet the embryo boat on the assembly line at a precise time. The Detroit influence also shows up in personnel policy. Chris-Craft hasn't hired a boatbuilder of the traditional type in years, but instead hires or trains specialists who perform a given function at a specific station in the line. However, there is still plenty of room for fine workmanship. Master Craftsman Victor Intihar, for example, is probably the nearest thing to the proud, painstaking oldtime boat-builder that a company could have and still operate on a production basis.
"I work on shaper forms, layouts, patterns and templates," says Intihar. "I can see the things I build on the boats that come off the end of the line, things like the keel shape and the basic lines of the hull. It is good work. And when the boat comes out, you feel good. It really looks like something." These thoughts are echoed by 28-year-old carpenter Roger Bratt, another typical Chris-Craft worker, who has the specific job of assembling frames and transoms. Bratt recently swept his arm down the long assembly line and said simply, "I built all those boats."
The 33-footer, however, has come a long way before it gets to Bratt, and has even farther to go before it emerges onto the shipping platform. It starts at the railroad end of the long Pompano Beach plant, where red and white mahogany from the Philippines, teak from Thailand, clear fir from the state of Washington and white oak from Indiana are unloaded and stored in a shed or kiln-dried until the proper moisture content of all the wood is reached. Then the production schedule assigns a series of swift carving operations to the mill. So efficient is the mill that, according to Plant Manager Jim Pocklington, "our only byproduct is sawdust"—plus a few scraps that go to high school manual-training classes or serve as aromatic fuel in Pocklington's fireplace.
As another timesaver, the ribs, traditionally bent on the boat, are steam-pressurized and bent on templates; actually they are overbent by a fraction so they will assume their correct position without strain. Meanwhile, paired lumber is pulled out of nearby storage bins and, through the use of jigs and forms, is turned into keels and transoms.
From this point, the keel, stringers and frames are bolted together, and thousands of screws are whirled home by electric screwdrivers to fasten the¾-inch side planking. Soon after, the raw hull is sanded and painted. And the moment the paint dries, an underwater-equipment specialist moves in to install shafts, struts and rudders.
Then larger units which have been under construction at other parts of the plant arrive at the line for installation. The cabin, the galley unit and the flying bridge and its molded fiberglass top are quickly set in place, as the 33-footer gradually assumes her final shape. At one magic moment near the end of the line she even acquires a voice when an electrician connects a wire and sounds a test blast of her chromium trumpets.
LAST O.K. FROM PRODUCTION
Finally, she passes the plant manager's last inspection and rides out into the sunshine, complete with anchor, side curtains, fire extinguishers, medicine cabinet, alcohol stove and even a plug for the sink—a symphony of mahogany and gleaming metal, ready to hunt for fish.
What Bill MacKerer, Jim Pocklington and approximately 150 craftsmen have designed, bolted, screwed, welded and glued into shape is a testament to the company's ability to provide the best specialized equipment at the least cost to the sportsman. To the average Chris-Craft customer, the other models, such as the 25-foot Cavalier cruiser, $5,245, currently the hottest item in the sales line, are no less remarkable in their own way. But to salt-water anglers, who tend to regard a boat primarily as a piece of fishing equipment, the particular combination of ingredients that make up the 33-foot sport fisherman is one of the greatest things that has happened since the gas engine first let a man run out into deep water where the big fish lie.
PHOTO
RICHARD MEEK
PHOTO
HEADING FOR OPEN SEA, 33-FOOTER GIVES SMOOTH RIDE TO FULL LOAD OF ANGLERS
PHOTO
PROUD FATHER A. W. MacKerer, designer of the new sport fisherman, watches his $26,175 babies roll off production line at Chris-Craft's Pompano Beach, Fla. plant.
PHOTO
FOR GUIDE TO COLOR PHOTOGRAPH ON PAGES 48-49, CHECK NUMBERS IN REPRODUCTION ABOVE AGAINST LIST OF ITEMS BELOW
1
2
3
4
5
6
7
8
9
10
11
12
13
14
15
16
17
18
19
20
21
22
23
24
25
26
27
28
29
30
31
32
33
34
35
36
37
38
39
40
41
42
43
44
45
46
47
48
49
50
51
52
53
54
55
56
57
58
59
60
61
62
63
64
65
66
67
68
69
70
71
72
73
74
75
76
77
78
79
80
81
82
83
84
85
86
87
88
89
90
91
92
93
94
95
96
97
98
99
100
101
102
103
104
105
106
107
108
109
110
111
112
113
114
115
116
117
118
119
120
121
122
123
124
125
MAKINGS FOR MASS PRODUCTION
1 Loft drawing of boat
2 Philippine mahogany frames
3 Chief Engineer E. L. Eckfield
4 Fishing chair
5 Engine box covers
6 Engine box slides
7 Engine box cleats
8 Deck hatch framing
9 Fuse-box cover
10 Portlight fillers and shims, forepeak locker floors
11 V-berth bottoms
12 Fuel tank chocks
13 Cockpit flooring
14 Bulkheads, flooring, panels and insulation for dinette, main cabin, head, bridge
15 Mahogany hull planking
16 Inner bottom planking
17 Bridge deck framing
18 White-oak keel (after end), mahogany sister keels, skeg, main stringers
19 Master Craftsman Victor Intihar, holding straightedge
20 Interior trim, fuel tank covers
21 Floor tile for deckhouse
22 Bulkhead and framing for forward compartment
23 Plant Manager J. R. Pocklington
24 Interior paneling and trim for head
25 Stainless-steel rubrail
26 Mahogany molding and trim
27 Forepeak locker door
28 Berth drawer
29 Overhead liner for deckhouse
30 Fuel tank cover
31 Engine room insulation
32 Forward deck beams
33 Outriggers
34 Metal bindings and hinges
35 Metal scroll initials
36 Rudders
37 Bilge pump and handle
38 Propellers
39 Shaft logs
40 Head and galley pumps
41 Rudder stuffing boxes
42 Shaft struts
43 Electric horns
44 Engine exhaust
45 Stanchion bases and miscellaneous deck hardware
46 Window supports
47 Bronze propeller shafts
48 Teak floor molding
49 Fuel tank sides
50 Molding
51 Engine-starting batteries
52 Hose clamps
53 Steering connections
54 Electric fuel pumps
55 Fresh-water rubber hose
56 Exhaust mufflers
57 Steering rods
58 Fire extinguisher and copper tubing for fresh-water system
59 Tool kit
60 Chris-Craft V-8 engine
61 Clutch-shifting unit
62 Water tank
63 Bronze keel bolts
64 Fuel tanks
65 Fishing-flying bridge
66 President H. H. Coll
67 Pilot chair
68 Cockpit ladder
69 Bottom bedding compound
70 Brass screws for hull fastening
71 Hull paint
72 Plate glass for deckhouse
73 Screws for engine mount
74 Electric connectors
75 Copper fuel lines
76 Steering cables
77 Outrigger snaps and lines
78 Boat hook
79 Rod racks
80 Side-mount rod holders and gimbals
81 Flush-mount rod holders
82 Chain for bilge drainage
83 Keel, stem and forefoot assembly
84 Gin pole bracket
85 Gin pole block and falls
86 Gin pole
87 Electric wiring
88 Chairman of the Board Harsen Smith
89 Fighting chair
90 Steering wheel, steering cables and turnbuckles
91 Clutch control
92 Throttle control
93 Intake scoops for engine cooling
94 Rudder control mechanism
95 Doors for stateroom, head, hanging locker and rope locker
96 Forward deck hatch screen
97 Sink and head
98 Portlight assembly
99 Lighting fixtures
10O Air vents
101 Medicine chest
102 Forward deck hatch assembly
103 Danforth anchor and line
104 Hand rails and belly rail
105 Swivel base for outriggers
106 Floor beams for cockpit
107 Life jackets
108 Fire extinguishers
109 Fog bell and range light
110 Berth and seat cushions
111 Ensign
112 Two-burner alcohol stove
113 Curtains and burgee
114 Folding canvas top
115 Galley and icebox assembly
116 General Sales Manager C. R. Burgess
117 Divisional Sales Manager E. L. Pickell
118 Deckhouse windshield and sideshield assembly
119 Deckhouse roof
120 Radio direction finder
121 Compass, automatic pilot control
122 Depth sounder and recorder
123 Radiotelephones
124 Auto pilot gyro compass and drive unit
125 Radio antenna