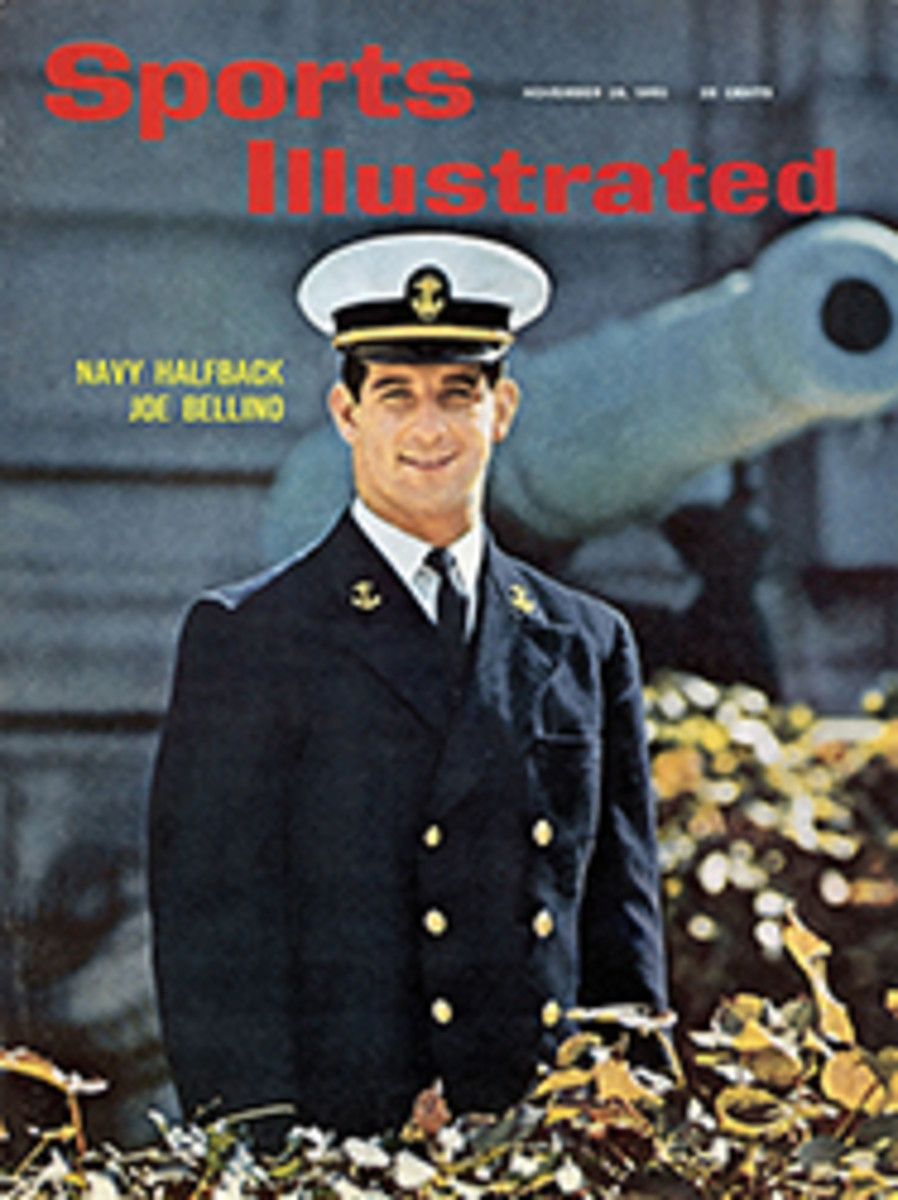
Mold of the future
The enormous slice of lemon meringue at right, standing in the main construction shed of the Pearson Corp. in Bristol, R.I., a few short years ago would have been classed as pie in the sky by most boatbuilders. Today it is a gleaming symbol of a fundamental change in their ancient art. This is a mold from which a boat will be born. In a few moments, workmen will begin lining the mold with fiber glass. Then they will coat the glass with a plastic called polyester, and within two weeks the chain hoist will reach down and pull from the mold the graceful hull of a 38-foot yawl of the new Invicta class. Six weeks later the Invicta, completely fitted for sea, will slide into the water to join a huge and growing armada of other vessels fashioned of glass by other boatbuilders across the nation. For, as incredible as it seems to yachtsmen raised in a tradition of wooden boats, at least 40% of the 400,000 vessels being produced in the U.S. this year will be of fiber glass. In some categories, such as de luxe outboard runabouts and cruisers, and in small and medium-size sailboats, fiber-glass construction is now almost universal. More significant than the number of glass boats, however, is the increasing length of the latest hulls.
Four years ago, when the fledgling plastic boat industry was first establishing itself (SI, Aug. 20, 1956), fiber-glass design was confined almost exclusively to small outboards, day sailers and other vessels that could be turned out virtually with a cookie cutter and that were not built to withstand the pounding a seagoing vessel must endure. Not a single ocean racer of fiber glass existed, nor was there a glass inboard power cruiser of comparable size. In fact, so little was known of the structural characteristics of fiber glass that the SPORTS ILLUSTRATED story reporting the early trend conceded that "structural problems and a tendency of polyester to fatigue at points of stress have limited mass production to craft of about 24 feet and under."
The breakthrough into large sailing craft occurred in December 1956, when Naval Architect Philip L. Rhodes completed the 41-foot ocean racer Bounty II. A descendant of a successful wooden hull, the fiberglass Bounty II was frankly experimental. "We encountered no serious bugs—just a surprise," recalls Rhodes. "We engineered for the tremendous strength of laminated glass but failed to take into account its elasticity. We soon found the whole bow was flexible. From then on isolated beefing up at points of stress took care of any problems. Fiber glass is here to stay. It has such wonderful properties that I don't see how it can be replaced except perhaps by another plastic, as yet undiscovered. And that one will have to be awfully good."
Just after the Bounty was introduced in California, Designer Bill Tripp's Vitesse yawls (since modified and renamed Block Island 40) appeared in eastern waters and, to the amazement of many yachting traditionalists, began winning races. The first major victory was scored in the 1958 Edlu Trophy Race by Fred Lorenzen's Seal. If the 40-foot centerboard yawl had been built of taffy candy with peppermint masts it could hardly have caused more of a stir. Yet only two years later, plastic yachts of seagoing size had won such universal acceptance that there was virtually no comment when 12 of them, all 40 feet or longer, made the rugged trek to Bermuda. And none of these boats showed the slightest sign of fatigue or strain.
It now appears there is no structural limit to the size vessel which can be built of glass. A 44-foot yawl from the board of Tripp is being produced by the Mercer Reinforced Plastics Corp., and the same designer is well along with the development of a 52-foot keel sloop for a group of Chesapeake Bay yachtsmen. John G. Alden & Co. is not only importing a line of 47-foot power cruisers fabricated by Halmatic Limited of England, but the first of their 67-foot power yachts was recently unloaded in Boston for interior finishing in the U.S. "There's no reason why we should not be able to build fiber-glass hulls 200 feet long or, for that matter to any length," says Patrick de Laszlo of Halmatic. "Beyond about 130 feet it is only the economics of the thing which would prohibit it."
Moving right along with the trend in civilian craft, the U.S. Navy is steadily increasing the number of fiberglass boats in the fleet. Whereas in 1950 there was not a single plastic vessel on its small-boat roster, by 1956 there were 900, and now there are approximately 1,400 (almost 25% of the total), ranging in size from 9-foot dinghies to 57-foot mine sweepers. The Navy also has a design completed for an 86-footer and appears convinced that plastics are suitable for vessels of 100 feet and possibly quite a lot longer. In fact, fiber glass is already performing handsomely in some of the Navy's submarines. Reporting on a conning tower fairwater—a streamlined outer covering—which had been in use for 2½ years on the U.S.S. Halfbeak, the Commander Submarine Forces Atlantic Fleet stated: "The ability of the plastic fairwater to withstand the stresses during a hurricane is most encouraging. No more conclusive evidence of reliability appears to be necessary."
Only recently I had visual proof of fiber glass's inherent strength and ability to recover from punishment when I inspected a Pearson Corp. Triton named Pywacket which had been mauled by Hurricane Donna. Pywacket was one of some 15 boats driven against a breakwater in Bristol harbor. Scattered along the shore at the base of the wall were remnants of wooden boats: keels and frames, random chunks of topsides and deck, sections of cabins. Yet Pywacket, when pulled up on the ways, sat jauntily on her cradle, virtually un-bloodied and certainly unbowed. A piece of her wooden rudder was broken off; there were hunks gouged out of her lead keel, and she had some deep scratches in her gel coat. But the integrity of her hull remained; she was watertight and she had not changed shape. There was nothing that plastic patches and a dab of epoxy paint would not make right. "Inside she's like a new boat," said a Pearson foreman, grinning. "Of course, we did have to rearrange the cushions and a few other things a bit."
In addition to its tremendous structural strength, fiber glass does not seem to deteriorate with age. In fact, the manufacturers of fiber glass are beginning to suggest that their product will last forever. "Forever is a long time," says Tony Cobb of Owens-Corning, a prime supplier to the boatbuilding industry, "but the first experimental boat built in 1944 still shows no change in the laminate."
With its manifold advantages, there is only one really valid reason why fiber glass is not even more widely used in the construction of large vessels. The reason is cost—specifically, mold cost.
Money for the mold
Nearly all fiber-glass boats are now turned out of molds, and the molding process, for the hull and deck of stock designs, though simpler and quicker than wood or steel or aluminum construction, still requires heavy equipment, exact engineering and a large initial investment of time and money. Virtually all U.S. manufacturers of boats between 25 and 45 feet use the same techniques: a wooden, so-called male "plug" is built—a full-size, minutely detailed dummy of the designed vessel. Next, fiber glass is laid over the plug to form female molds, for the hull and the deck. The boat itself is built up inside these female molds—gel coat first, containing the desired color (as shown in the photograph on page 61), then layers of glass mat and roving (a coarse material like burlap), bonded by liquid polyester resin, which soon hardens. Later the deck is fastened to the hull, again by fiber-glass laminate, forming a structure of great strength and watertight integrity.
Unfortunately, the plugs and other preliminary steps in molding can cost almost as much as a finished wooden yacht of similar dimensions. According to Breckenridge Marshall of American Boatbuilding Corp., which builds the Block Island 40, "a single hull to the Bermuda Rule limit of 73 feet would be incredibly expensive, costing perhaps three times as much as wood. And the breaking point where the price would be comparable would be at about eight units."
In the case of the Invicta class, Everett Pearson says: "We will probably write off the cost of the mold over 10 to 12 units to keep the individual cost down for the buyer, but we could write it off with six hulls and still produce a boat competitive in price with comparable wooden boats."
In time, the cost factor in mold building should yield to technological advances. Meanwhile, despite the initial expense, fiber-glass boats are taking a larger and larger bite out of the market. The only remaining pocket of resistance to glass is among the big builders of power cruisers. Chris-Craft and Owens, the giants of the stock power cruiser industry, have not switched to plastic, although the latter will soon offer at least one smaller fiber-glass model.
"Those two just about own that part of the market," commented a rival builder. "It hasn't been necessary for them to change; they're doing all right as it is. But a situation might develop like Detroit and the compact cars, and they might find themselves losing enough sales so that public demand would force a switch."
One boat that may force the switch is Richard Bertram & Co.'s forthcoming 31-foot version of the Moppie design (SI, April 25), which won this year's Miami-Nassau powerboat race in such spectacular fashion. Another is the Hatteras 41, a combination sport fisherman and cruiser, and a third is Alden's 47-footer by Halmatic.
Today, four years after its first strong step into the boating industry, fiber glass seems more than ever the perfect material for boats. Unfortunately, some excesses have been committed in its name by manufacturers who were more promoters than skilled designers or builders. And in these cases complaints seem to stem from faulty construction rather than faulty materials. But as these fringe builders improve their standards—or are eliminated—and cheaper, quicker molding techniques are developed, it may well be that the wooden boat will become the marine curiosity of the future. Captain R. S. Mandelkorn, former comptroller of the Navy's Bureau of Ships, speaking unofficially but perhaps prophetically, declared that once standardization in construction is achieved, the wooden boat, for Navy purposes, would become "as obvious an anachronism as the steam locomotive." Another strong vote comes from America's Cup designer Olin Stephens. Asked recently what sort of craft he would design for himself, he replied, "I'd probably go along with the rest of the world and have a fiber-glass boat."
I believe I would, too.
PHOTO
RICHARD MEEK
READY FOR PRODUCTION, Everett A. Pearson of Pearson Corp. stands in keel well of mold just before workmen start laying in fiber-glass mats for hull of Invicta yawl. Yellow color is gel coat which will give boat its final hue.
PHOTO
OUT OF MOLD AND RIGGED FOR SEA, 38-FOOT INVICTA IS FIRST-CLASS OCEAN RACER
PHOTO
BLOCK ISLAND 40 (ABOVE) IS ONE OF 12 FIBER-GLASS BOATS THAT RACED TO BERMUDA
PHOTO
HATTERAS 41 IS FIRST BIG PLASTIC POWERBOAT TO MAKE DENT IN CRUISER MARKET
PHOTO
ALDEN'S 47-FOOTER MAY HELP PUSH OWENS, CHRIS-CRAFT INTO GLASS PRODUCTION