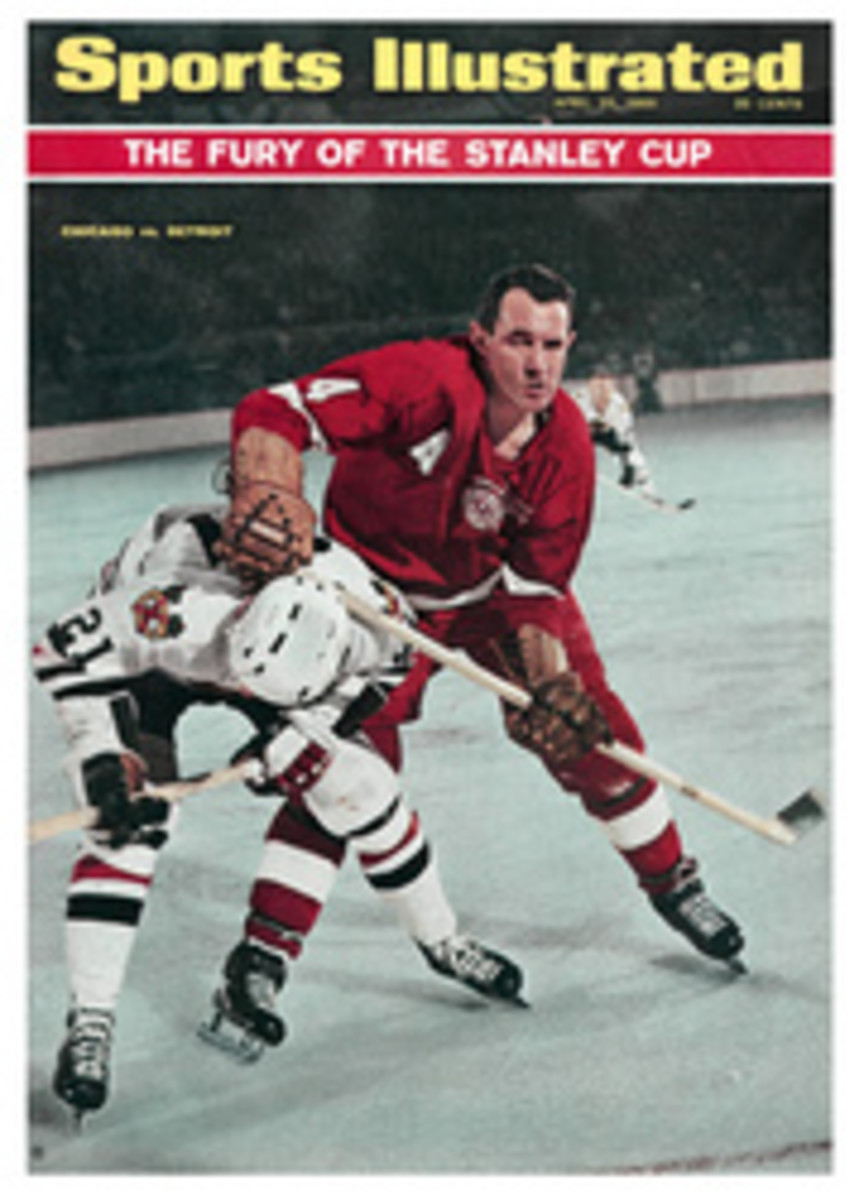
Now it's the waltz-me-around-again Wankel
"The trouble with engines, by and large, is pistons. Pistons go up and down. This would be all right if boats and automobiles ran on legs, which also go up and down. But propellers and wheels, on which boats and cars depend for their movement, go around. Thus most of the ingenuity (as well as most of the moving parts) in an engine designed to drive a boat or a car is aimed at translating the up-and-down movement of pistons into the rotary movement of the drive shaft.
Motor manufacturers have known for a long time that their problems would be vastly simplified if they could find a piston that would spin instead of bouncing. But the perfecting of such a design has eluded engineers almost as long as the perfecting of a perpetual-motion machine.
Now, however, Outboard Marine Corporation believes it has found a rotating piston motor that really works. It was invented by Felix Wankel, a German mechanical engineer who was once in the employ of Hermann Göring's Luftwaffe. Wankel got to thinking seriously about rotary pistons when he was working on rotary valves and sealing systems for Germany's burgeoning air force before World War II. His ideas had plenty of precedent. Designs for dozens of different versions of the rotary combustion engine were lying in the files of nearly every engine manufacturer in Europe. Soon after the war ended, his purpose bulwarked with the knowledge of all those former failures, Wankel set up a workshop of his own in a boathouse on the banks of Bavaria's placid Bodensee in Lindau.
West Germany was then just beginning its industrial recovery, and few German engine manufacturers were anxious to change pistons in midstream. But one small maker of sewing machines in the Black Forest was eager to expand into automobiles—provided it could find a gimmick to get started with. Wankel's notion of a rotary engine seemed just the thing, and the firm of NSU-Wankel was born.
After a number of trials and errors, the new combine at last produced a rotary that worked and gave it a public demonstration—not, however, in a car, but in a boat. Mounted in a miniature craft, the little Wankel towed a water skier around a German pond at 28 mph as smoothly and silently as one of its maker's sewing machines.
By 1958 the Wankel principle had advanced far enough to interest Curtiss-Wright, one of the world's biggest manufacturers of airplane engines. Over the years Curtiss-Wright has paid out some $5,200,000 for the sole right to manufacture Wankels in North America plus the sole right to develop Wankels for aircraft all over the world. One by one, other big-name engine manufacturers got into the act. In Japan, Toyo Kogyo bought the right to make Wankels in its part of the world. Daimler-Benz is now developing both diesel and fuel-injector Wankels up to 180 hp. The Perkins group in England is working on an air-cooled outboard.
Now America's Outboard Marine, a company so huge it includes the two biggest names in outboard boating—Evinrude and Johnson—has put up more than a million dollars for the right to make Wankels for boats.
Whether or not the prediction of the Stanford Research Institution that half the compact cars in the world will be rotary-powered by 1972 comes true, it is certain that many if not most outboard motorboats will be. Whatever else it may be good for, the Wankel seems almost perfect for outboards. It is constructed of only two moving parts: a rotor and a drive shaft to which the rotor is directly connected, without the intercession of any rattling crankshafts, connecting rods or bearings. Right there three-quarters of the headaches of motor design and maintenance have been banished.
The Wankel rotor, which takes the place of the piston in a reciprocal engine, is a thick, three-cornered slab of machined metal shaped rather like a Valentine's Day heart except that all three of its sides are identical. Just as a piston moves up to compress a mixture of gas and air in the cylinder of a reciprocal engine and is in turn forced down again by the explosion of the mixture, the rotor in a Wankel slides around a specially shaped chamber, first compressing, then being pushed by that same explosive mixture. The chamber that takes the place of a cylinder in the Wankel is shaped like a very thick-waisted hourglass. It is known technically as an epitrochoid. Thanks to an eccentric fixed to the drive shaft, the rotor is made to move around this chamber in a waltz-like motion somewhat comparable to the combined rotation and revolution of the earth in space.
As the rotor dances, it keeps each of its three corners pressing against the walls of the epitrochoid chamber in a gastight seal. Between each of its three sides and the walls of the chamber, therefore, there is a crescent-shaped space which grows fatter and thinner as the rotor moves round, just as the empty space in a cylinder grows smaller and bigger as the piston moves up or down.
There are no intake or exhaust valves in a Wankel and hence no need for a camshaft or tappets to actuate them. As the rotor turns, one of its corners passes an intake port. As it moves on, the crescent chamber expands and the fuel mixture is sucked in. The next corner of the rotor then moves on to seal up the intake port and the crescent chamber becomes smaller and smaller, compressing the gas mixture until it is dragged past a sparkplug. The ignition causes an explosion that drives the rotor on past the exhaust port through which the spent gases are flushed away. A fraction of a second later the corner has reached the intake port again, and the whole cycle begins once more.
Meanwhile, of course, the same process is going on at progressively different stages on each of the other two sides of the rotor—a circumstance that has led shrewd German tax assessors to classify the Wankel as a "three-cylinder engine" although its German manufacturers stoutly insist—for tax purposes—that it is only a "one-cylinder engine."
Whatever its tax status, the Wankel delivers its driving power in a smooth and unbroken continuum whose contrary forces are so balanced as to make it almost completely vibration-free. This, in addition to the simplicity of its design, permits normal compression with incredible lightness of construction. Curtiss-Wright reports a marine Wankel with a power-weight ratio of only half a pound per horsepower.
There is not much more that Outboard Marine or any other manufacturer can do for the complex power plants they now hang on transoms except to make them bigger and more complex. With an enormous investment in the status quo, OMC insists that it has no intention of scrapping all its current designs in favor of the Wankel. But it seems a safe million-dollar bet that it won't tuck that tidy Wankel away in the attic and just forget it.
ILLUSTRATION
WANKEL'S TRIANGULAR ROTOR, which takes the place of a piston in an ordinary engine, spins around its combustion chamber on a shaft set slightly off-center. As it turns, crescent-shaped spaces at each of its sides expand and contract to suck in and then compress the explosive gas.