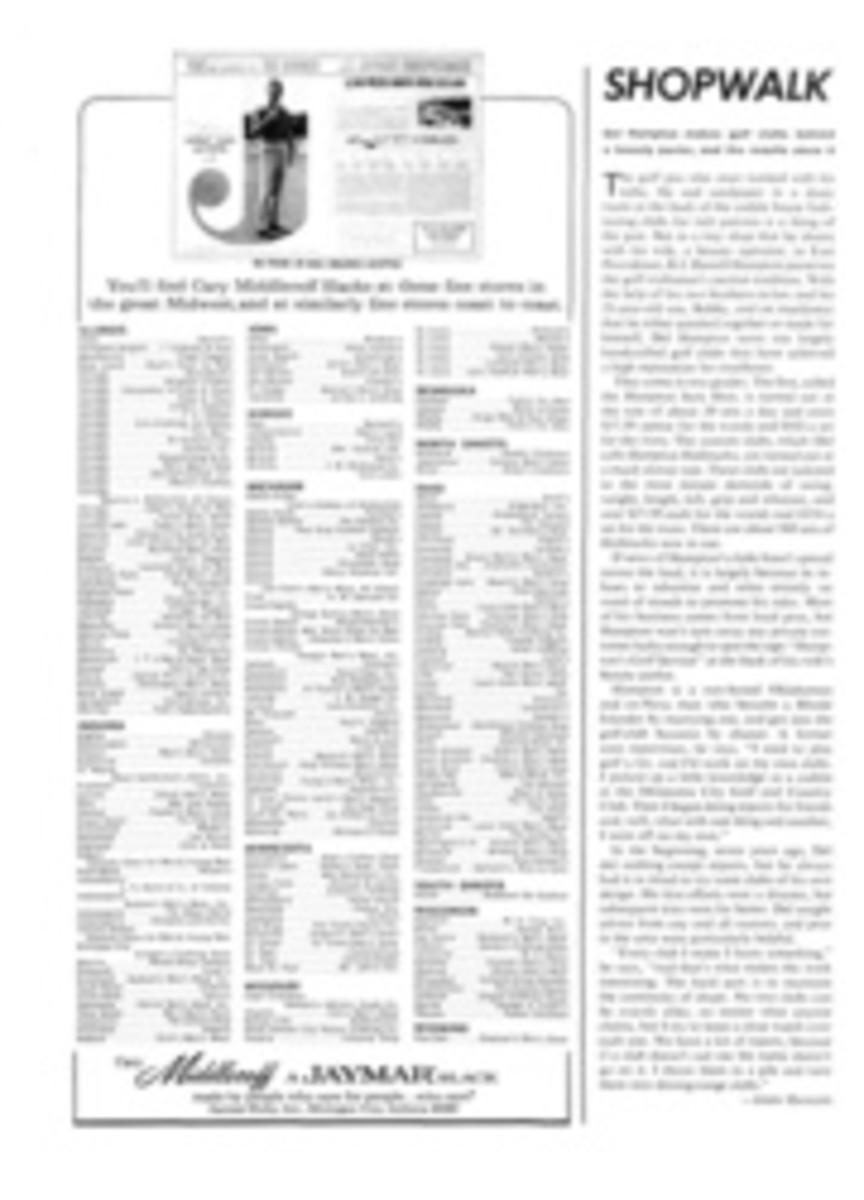
Del Hampton makes golf clubs behind a beauty parlor, and the results show it
The golf pro who once worked with his lathe, file and sandpaper in a dusty room at the back of the caddie house fashioning clubs for rich patrons is a thing of the past. But in a tiny shop that he shares with his wife, a beauty operator, in East Providence, R.I. Darrell Hampton preserves the golf craftsman's ancient tradition. With the help of his two brothers-in-law and his 21-year-old son, Bobby, and on machinery that he either patched together or made for himself, Del Hampton turns out largely handcrafted golf clubs that have achieved a high reputation for excellence.
They come in two grades. The first, called the Hampton Sure Shot, is turned out at the rate of about 20 sets a day and costs $17.50 apiece for the woods and $102 a set for the irons. The custom clubs, which Del calls Hampton Hallmarks, are turned out at a much slower rate. These clubs are tailored to the most minute demands of swing, weight, length, loft, grip and whatnot, and cost $27.50 each for the woods and $154 a set for the irons. There are about 500 sets of Hallmarks now in use.
If news of Hampton's clubs hasn't spread across the land, it is largely because he refuses to advertise and relies entirely on word of mouth to promote his sales. Most of his business comes from local pros, but Hampton won't turn away any private customer lucky enough to spot the sign "Hampton's Golf Service" at the back of his wife's beauty parlor.
Hampton is a raw-boned Oklahoman and ex-Navy man who became a Rhode Islander by marrying one, and got into the golf-club business by chance. A former auto repairman, he says, "I used to play golf a lot, and I'd work on my own clubs. I picked up a little knowledge as a caddie at the Oklahoma City Golf and Country Club. Then I began doing repairs for friends and, well, what with one thing and another, I went off on my own."
In the beginning, seven years ago, Del did nothing except repairs, but he always had it in mind to try some clubs of his own design. His first efforts were a disaster, but subsequent tries were far better. Del sought advice from any and all sources, and pros in the area were particularly helpful.
"Every club I make I learn something," he says, "and that's what makes the work interesting. The hard part is to maintain the continuity of shape. No two clubs can be exactly alike, no matter what anyone claims, but I try to keep a close watch over each one. We have a lot of rejects, because if a club doesn't suit me the name doesn't go on it. I throw them in a pile and turn them into driving-range clubs."