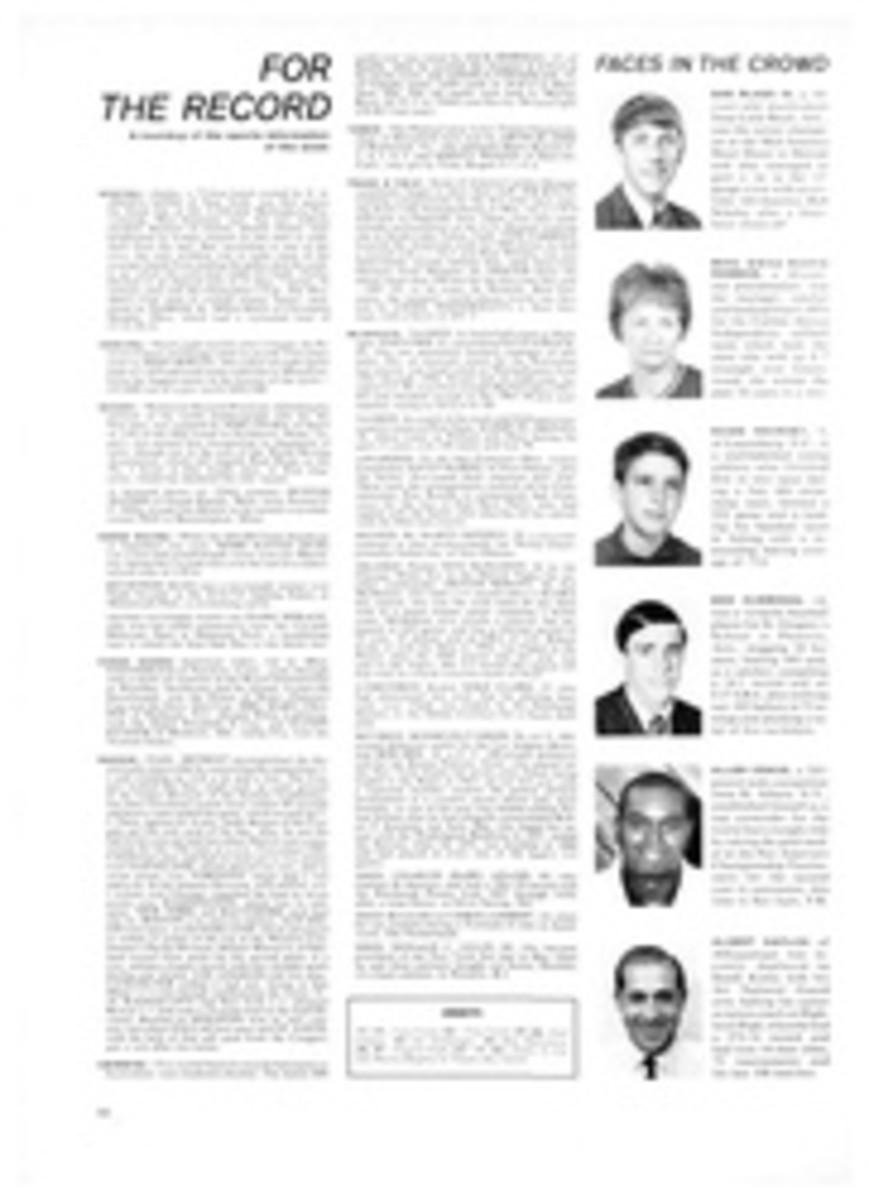
What can a girl give a hustler who has everything? Answer: a jeweled Ginacue
The best pool cues in the U.S. today are made in a garage at 15153 Greenleaf St., Sherman Oaks, Calif. There Ernie Gutierrez combines ivory, silver, gold and such exotic woods as African snakewood and ebony to make cues that more than 50% of the top professional billiards and pool players swear by.
"In a cue by Ernie the balance is always mellow," says Marvin Henderson, a Stardust Open winner, explaining why he will use no other cue in tournament play.
A custom cue consists of two pieces of wood, the shaft and the butt, fashioned separately so they can be screwed together. The whole cue weighs around 20 ounces and is 58 inches in length. Each piece is cut, then turned to proper dimensions on a lathe. The task appears simple, yet its execution demands many different skills, a feeling for wood, ivory and other materials and, most important, a craftsman's patience and temperament. A good cue has to have balance, solidity and must not vibrate unduly or "ping" after the hardest strokes. In billiards, particularly, a shaft lacking "heart" will make it difficult to control the ball.
Gutierrez, who calls his product Ginacue, after his daughter Gina, claims to be the only cuemaker who can actually cut a cue to personal specifications. His long suit is an uncanny ability to duplicate the feel of any cue he touches. Ernie did not come by his skill easily. He began working with wood at the age of 10 in Bogotà, Colombia, where he helped his father make castanets by hand. Ernie came to the U.S. at 16 and got a job with a ballpoint-pen manufacturer. He soon tired of that.
In 1963 Ernie began playing pool. Fascinated by the game, he paid $100 for one of the leading custom cues then made. After a few months it began to come apart in his hands and when Ernie asked the maker to repair it the man demanded another $30 before he would touch the cue. Ernie decided to fix it himself. As he worked he became intrigued by the complexity of what seemed so simple. He set the custom cue aside and decided to make one of his own.
In the five years that followed Ernie made more and more cues, and his reputation circulated as artists like Minnesota Fats, Eddie Kelly, Ronnie Allen, Danny DiLiberto and Richard Florence began to use them. Florence, at 24 probably the hottest young player on the professional circuit today, finds it difficult to pinpoint why he uses a Ginacue: "In my game, the cue does the work. Ernie's cues feel like they're part of you. The other cues feel different. I don't know why. Ask Ernie. He makes them." Ernie just smiles.
Watching Ernie work, one is reminded that genius often consists of the ability to apply endless patience. When Ernie sets a mother-of-pearl cloverleaf into ebony the lines around the pearl flow smoothly and break cleanly. Not long ago Ernie decided he should have a special personal cue around the shop so that visitors asking to see the differences between his basic and more elaborately carved models could get a notion of the best. For several months he walked around with chunks of ivory in his pockets to keep them warm and make them easier to work with. For a basic motif Ernie chose to use Colombian silver in a classical baroque design. Some 1,900 work hours later Ernie had an ivory-and-silver cue for which he has turned down offers of $4,000.
Ernie's skill was tested again when the board of directors of Share, a group of Hollywood matrons, was looking for a gift for an important man who had helped with three charity events. What, the girls asked Marvin Hime, a local jeweler, could they give Dean Martin, the man who has everything? Hime considered his own resources and the skills of his craftsmen, then remembered something he had heard at a manicure parlor about a guy who made a better pool cue than anyone else. A few minutes later he was on the phone talking to Ernie.
In a marriage of talents Hime contributed some precious stones (a ruby, a sapphire, an emerald and a diamond), a 3½-ounce gold bar, the skill of his goldsmith and a basic design. The rest was up to Gutierrez. Ernie worked 16 hours a day for a week on the Dean Martin cue. The design called for four gold panels inlaid around the butt, each Florentined panel noting a separate aspect of Martin's interests: crossed champagne glasses, golf clubs, comedy-tragedy masks and a tiny plaque expressing the gratitude of the girls from Share for Martin's contributions. The cue was presented at the group's last annual party. It left a flabbergasted Dino without a word to sing except in praise, after he got the cue home to his private table and tried it. Ernie estimates that it would cost over $1,300 to duplicate Martin's cue.
Ernie's basic model is slightly less expensive. It comes in plain white maple and costs $70. Outside of the eight-pronged scoring design that is another unique characteristic of a Ginacue, the quality of Ernie's most expensive sticks is present in the basic model's balance, feel and durability.
Ernie mixes his own finish, using a secret ratio of shellac to silicone that gives a Ginacue its unusual durability. The worst enemy of a finished cue is a drastic change in temperature. According to Ernie, the most damaging thing you can do to a pool cue is to leave it in a closed car.