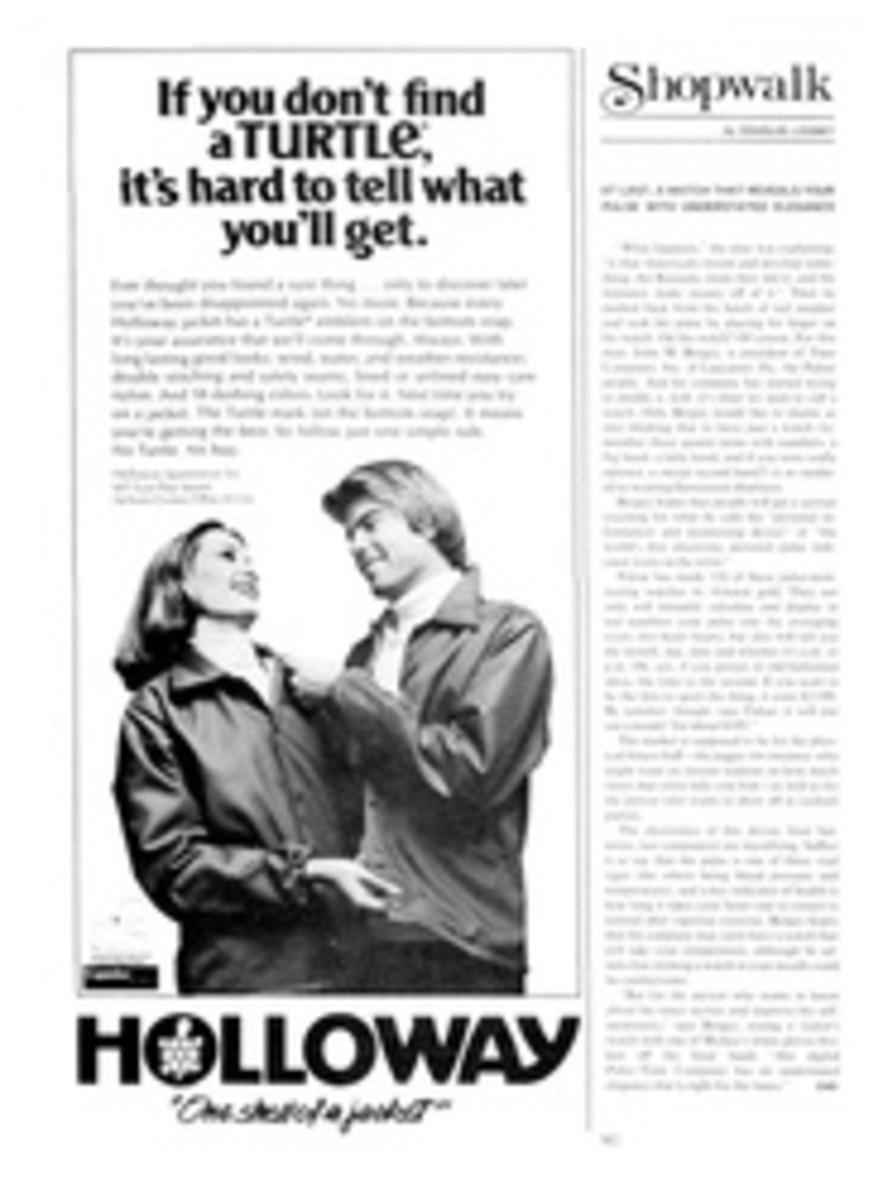
IF YOU'RE LOOKING FOR A HAND-BUILT BIKE, BE READY TO HAND OVER $1,000
There are perhaps 50 builders of custom-made bicycles in the U.S., but only one of them has been compared to Antonio Stradivari. He is Bill Boston, 30, of Swedesboro, N.J., a rural community of 2,300 near Philadelphia. "He builds a bicycle," says one admirer, "with all the care and skill of a Stradivari fashioning a violin."
Boston smiles. "I don't have an Italian name," he says, "but I'm better with my hands than the average person." And he holds out his hands as if for inspection.
Indeed, Boston is a superb craftsman who sets out to put together the ideal: that is, as technically perfect and comfortable a machine as possible for each of his customers. In the five years he has been building bikes, Boston claims never to have made two that were exactly alike. Tandems are the biggest challenge, because they must fit two people usually differing in size. A fitting at Boston's workshop in an old garage on Franklin Street takes 2½ hours for singles and up to eight hours for tandems. Boston's first question to a prospective customer is, "What do you want to use the bike for?" Most of his patrons are tourers, and they come from all over the country. They range from the New York executive who enjoys a Sunday ride in Central Park to the retired couple from Schenectady, N.Y. who are planning an extensive bike tour across Europe, or the young fellow who wants the wind in his face.
To determine the proper fit, Boston has designed a tandem fitting stand. "The only one of its kind in the world," he says. While a customer sits on the stand and pedals furiously. Boston adjusts tubes to establish proper lengths and height, and with the help of a calculator he figures the correct angles. This and other pertinent details are entered on a "custom-frame order form." together with the client's vital statistics, which include the length of his arms, forearms and legs. One gets the feel of a medical checkup.
Boston bronze-welds the frames from Reynolds 531 tubing, a manganese-molybdenum steel alloy he imports from England in different thicknesses. "The walls are thicker at the ends than in the center to give the bike high strength while keeping its weight down," he says. "A heavy rider or a racer who wants a stiff bike needs heavier tubing." For a comfortable ride, Boston adjusts the length of the handlebar extension and the top tube. A tourer frequently wants to be more upright than a racer." For a start, when you put your elbow against the front of the saddle, you should be able to reach the handlebar with your fingertips," he says. "If the bar is too far away, the bike will be unstable."
Once Boston has established the dimensions of the frame, he helps his customers select from a wide variety of the finest components built in the U.S. and abroad. He has never used upright handlebars and thinks the best dropped bars are made by Cinnelli of Italy. Boston recommends an English Brooks saddle or, for women, a wider French Ideale TB-14. There are approximately 42 sidepull and 25 centerpull brakes to choose from. Campagnolo's sidepulls are the best. For tandems he suggests cantilevers, very powerful brakes mounted on both sides of the wheel. Most bicycles come with cup-and-cone bearings, which get dirty and require maintenance. Boston uses precision-made sealed bearings from Phil Wood & Co. in Los Gatos, Calif., which do not have to be cleaned and readjusted.
Boston takes a week to put a singles bike together and three weeks to finish a tandem. Then he hand-sprays the machines with lustrous Du Pont paint. Among his customers' favorite colors are electric blue, dark green, mahogany brown, black and burgundy red.
Boston's singles go for $1,000 while the tandems start at $1,600. He has built a bike with a 29-inch seat tube for a 6'9" man and one with a 16‚Öû-inch tube for a 4'11" woman. "I love to solve problems," he says. "I would get bored without them."
Boston worked as a chemical lab technician for Du Pont, then spent four years in the Navy as a quality assurance inspector of jet engines before returning to Du Pont. While at sea on an aircraft carrier, he was often seen riding a Japanese unicycle on deck. When he went home to Swedesboro, he bought an English Holdsworthy bike, at the time considered by many to be the best on the market. Boston decided he could build something better. He went to England to learn his trade from small builders, because "I wasn't going to become a big manufacturer." Excellence has always been more important to Boston than affluence. Now he builds about 50 cycles a year and, much like any other artist, feels that every one still belongs to him long after it has left his shop. Because Boston always has a backlog of orders, his customers, who often become his friends, frequently wait six months for their bikes. What he likes to see most is a happy pair "riding off into the sunset" on one of his tandems. One couple had their wedding picture taken on their new tandem last year.
"I don't give anybody a bill until the bike has been tested by the customer," he says. "They ride for a mile and come back with that big grin on their faces. It is almost better than the money."