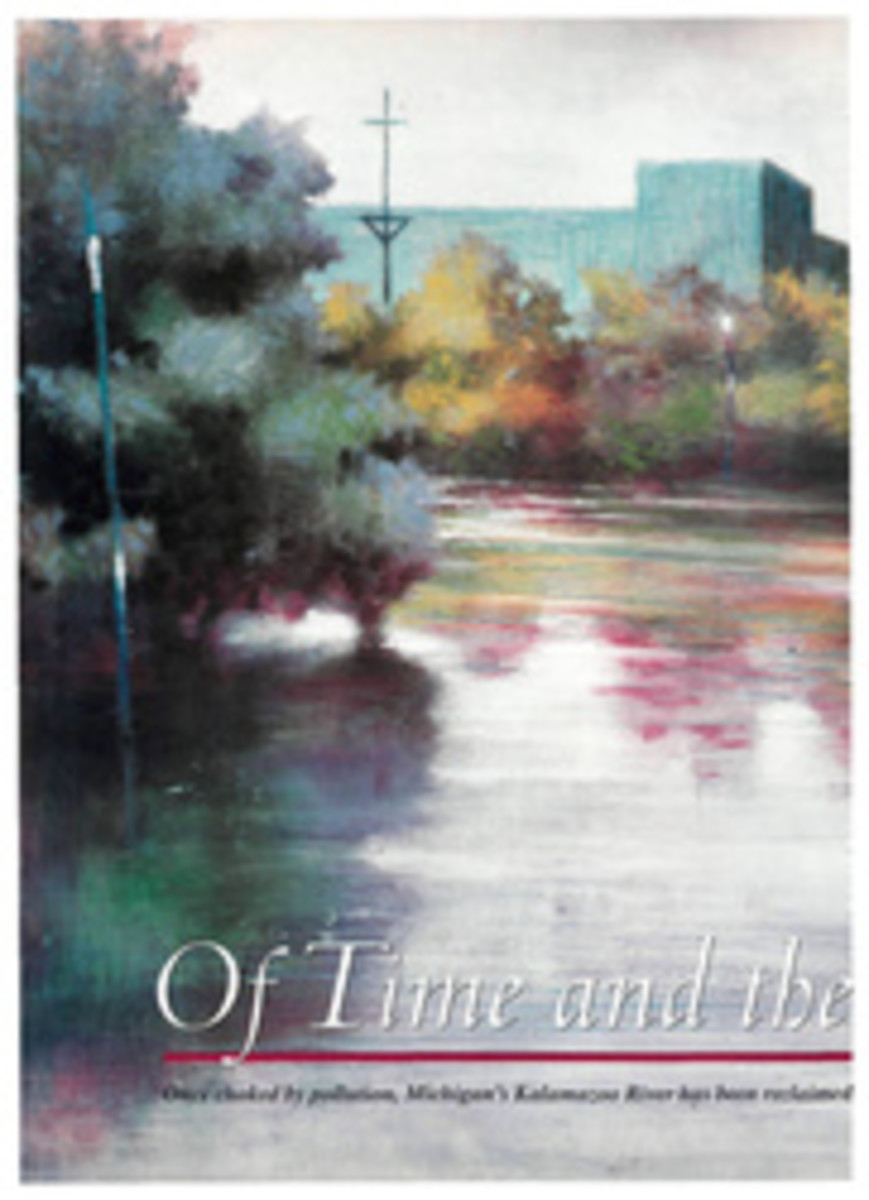
END OF AN ERA
A hot, sunny Cape Cod Sunday was giving way to the softness of evening. The visiting Cotuit Kettleers began their batting practice as a few fans settled into the stands at McKeon Field in Hyannis, Mass., for the season opener of the Cape Cod League, an amateur summer league for leading pro prospects. Rich Juday, a Kettleer outfielder who plays for Michigan State, took his first round of eight swings. He hit a couple of line drives and a few grounders and sent one ball to deep leftfield.
Juday finished his turn and walked behind the wire batting cage to await his next round. "The ball just doesn't seem to go anywhere," he said to teammate Greg Haeger, a University of Michigan first baseman. "It still feels as if the bat's dead."
Haeger shrugged and said, "We'll get used to these things. That's what we're here for."
These things were the bats—wooden baseball bats—and on this night, for the first time in either of their lives, Juday and Haeger would step to the plate in an official game with a wood bat in hand. Both had played Little League, youth league, high school, American Legion, summer league and Big Ten baseball, and until now, as 20-year-olds entering their junior years in college, they had always hit with aluminum bats. "We've been working out for four or five days, trying to get used to wood," said Juday. "There have been a lot of broken bats, sore hands and blisters. The coaches are telling us, 'You have to hit with the label this way—either up or down.' Most of us didn't know what the label on a wooden bat meant."
For more than 20 years. Major League Baseball has helped fund eight amateur summer leagues, including the Cape Cod League. This season, baseball gave the league $74,000 to offset the costs of balls, umpires, scorekeepers and—most costly of all—wooden bats. Because it is one of only three of those amateur leagues to use wood, the Cape Cod League attracts some of the nation's best college players. "It's like a professional internship," says Central Michigan second baseman Darin Dreasky. "You know scouts are watching because they want to see how you make the adjustment from aluminum to wood. We all want to play pro ball, and pro ball is a wood game."
For now it is, but it won't be for long. Pressed by economic forces, the low minor leagues are likely to begin playing with aluminum bats within two years. By the turn of the century even the majors will probably have put down the lumber and picked up the metal. Like it or not, the crack of the bat is inevitably being replaced by a ping.
Some 70 miles up the road from Hyannis, the day after the Kettleers' season debut, Boston Red Sox outfielder Mike Greenwell was sorting through his bats. "I ordered mine the second week of spring training and finally got the shipment the first week of June," said Greenwell. "I've used Dwight Evans's bats, Ellis Burks's bats, Jody Reed's. I guess it's just not as simple as saying, 'I need two dozen bats,' and having them delivered a week later."
"Greenwell is a .326 lifetime hitter, the [1988] MVP runner-up," says Toronto Blue Jay assistant general manager Gord Ash. "And he's having trouble getting bats. Imagine what it's like for guys in the A leagues and kids in rookie ball, who are using wood for the first time and breaking a bat a day. The problems are acute in the minors, in terms of cost, availability and quality."
Cost is the biggest reason the wooden bat is an endangered species. Wood bats break; metal bats don't. It's as simple as that. The college game came to grips with this harsh reality in 1974, when the NCAA approved the aluminum bat. "I wish we were all subsidized by the major leagues and could have wood throughout the game," says North Carolina coach Mike Roberts. "But it's economically unfeasible. In college, each player gets an aluminum bat
, and most of the players use that one bat the entire season. Over the course of the fall and spring seasons, we'd probably use more than 50 dozen wooden bats." At $14 per bat, that's a difference of about $7,500 a year, a figure no college athletic director can afford to ignore.
Los Angeles Dodger hitting coach Ben Hines is concerned about the availability of wood for bats. "If good wood is getting harder and harder to find for the top major league hitters, then you see what minor league players have to use. College, high school and Little League teams would be getting sawdust glued together if they still used wood. You're going to see aluminum creep farther and farther up the professional pyramid."
"We've been told to prepare for a severe wood shortage over the next few years," says Bill Murray, director of operations for Major League Baseball and chairman of the rules committee. "We may have to start thinking about an alternative to the wood bat."
"I certainly see a time in the not-too-distant future when everyone will be using some alternative bat—aluminum, graphite or some composite," says Jack Hillerich, the third-generation president of Hillerich & Bradsby, which, because of its Louisville Sluggers, has been synonymous with baseball bats for more than 100 years. "A wood bat is a financially obsolete deal. If we were selling them for $40 apiece instead of $14 or $16.50 I the company's prices for minor league and major league bats I. then we'd be making a sensible profit. But we aren't. We can't charge that much. The time will come when even the majors will use aluminum or graphite."
Hillerich, whose company's bat production is now more than 50% aluminum, says that the availability of wood isn't the primary cause for concern—at least for H & B, which grows its own timber. But other batmakers do experience shortages. And all of them, Hillerich says, have found wood bats to be an increasingly inefficient proposition.
"While once we were making seven million wood bats a year for all levels of baseball, now we're making a million and a half, 185,000 of which go to the major leagues," says Hillerich. "Major leaguers want specific orders, so we make three orders [one dozen bats per order] for one player, then shut down the operation. Then we make three more for another player, and shut it down. That's impractical, and it's highly expensive."
All of the bat companies (H & B, Rawlings-Adirondack, Worth and Cooper) have had trouble filling wood-bat orders this season. "I'm having to stop taking orders," says H & B salesman Paul Shaughnessy, who services several major league teams.
"No one even wants the major league business anymore," adds Chuck Schupp, H & B director of professional bat sales. "We do it but partly because of the 100-year relationship we have had with baseball. When we make a bat, we use 40 percent of the wood, at most. If we sell the billets to other industries, nearly 100 percent is used."
Meanwhile, major league players have raised a chorus of complaints about the quality of the wood in the bats they're getting. "You can get an order of 12 bats, and only one or two of them have the good grain," says Kansas City Royals outfielder Willie Wilson. "No matter how good you are, it's hard to get enough quality bats," says Texas Rangers outfielder Pete Incaviglia, who goes through nearly 40 dozen bats a season.
Hillerich refutes the players' claims about the quality of the wood. "Most of them don't know what they're talking about," he says. "We can come up with the best white ash you'd ever see. Players do a lot to break bats. They shave the handles, for instance. That destroys the product." At the same time, major leaguers have shown an increasing affection for the lighter, thinner-handled big-barreled bats, which break more easily (witness the exploding bat in the hands of the Mets' Gregg Jefferies on the cover).
The bottom line on the wooden bat is that the bat companies don't want to make them, and the pros are having trouble getting good ones. The alternative is clear. Says Ash of the Blue Jays, "They should use the aluminum bat in a rookie or low A league next season and see what happens." Adds Murray, "It's a subject baseball has to take a long, hard look at in the next year."
Anyone who's thirtysomething or older and grew up playing baseball remembers the Louisville Sluggers and Adirondacks that were the staples of the game. Every young ballplayer imagined swinging the bat hard enough to duplicate the gunfire crack that Mickey Mantle and Frank Howard produced when they smacked the ball just right, the crack you could hear on the radio above the din of 40,000 fans. Today, though, on sandlots across America, that sound has given way to the metallic ping reminiscent of a golf ball ricocheting off a flagpole, an aesthetically inferior experience, to be sure.
In a sport as steeped in romance as baseball, that ping alone is enough to make purists resist the aluminum bat. More important, however, wooden bats and aluminum bats are very different beasts, and the evolution from one to the other is changing the game in significant ways.
How different are the two bats? Seattle Mariners rookie Ken Griffey Jr. was recently asked to name the biggest difference between high school baseball and the majors. "The wooden bat," he quickly responded. Says Dodger slugger Kirk Gibson, "Wood bats drove me crazy at first. I must have busted hundreds of them." And Boston's Greenwell says, "It took me two years to adjust to wood. My hands ached. I had a bone bruise the shape of a horseshoe on my palm that I couldn't get rid of."
"If you hit a ball right with a wooden bat, it'll go about the same distance as a ball hit with aluminum," says Seattle catcher Scott Bradley, who wielded aluminum during his college days at North Carolina. "But with wood you have to hit it right. You have to use your hands, get the bat head out and hit it on the sweet spot. If you get jammed or hit it off the end of the bat—unless you're Bo Jackson or Jose Canseco or Kevin Mitchell—the ball doesn't go anywhere, you often break the bat, and your hands hurt.
"With aluminum, you can make contact most anywhere on the bat and get the ball through or over the infield. Watch a college game and see how many hitters get jammed and still hit flares into the opposite field. The center of balance is different, and when you've been swinging one kind for 20 years, there's a big change."
When Texas Rangers general manager Tom Grieve was managing a rookie league team in 1982, he used to hand all his players a wooden bat and take them to a nearby telephone pole. "I had each kid tap the bat against the pole until he found the spot on the bat where he couldn't feel any vibrations coming down to his hands," says Grieve. "That's the sweet spot, and on an aluminum bat it's larger than on a wooden one. By finding the spot on a wood bat where he has to hit the ball, a kid can see what he's dealing with before he starts the adjustment process. With an aluminum bat most kids can take the same swing at every pitch. When they see that they have to hit the ball on a certain spot on a wooden bat, they find out they have to swing differently, according to the pitch."
"What you see with the aluminum bats are a lot of long, sweeping swings because you can hit the ball most anywhere on the bat and drive it anywhere in the ballpark," says Oakland A's player-development director Karl Kuehl.
Aluminum bats have still another advantage over their wood counterparts. "The weight difference between aluminum and wood bats makes it a lot easier to generate bat speed with the aluminum, and bat speed is what determines power," says Oakland hitting coach Merv Rettenmund. "Most 34-inch aluminum bats weigh 29 or 30 ounces [while a standard 34-inch wood bat is two to four ounces heavier]. That's a big difference."
In their debuts with wood on Cape Cod, Juday and Haeger each went hitless as Cotuit lost the opener to Hyannis 3-1. "The scores are pretty low for the first few weeks," says Cotuit manager Pete Varney. "Most of the kids make the adjustment in four or five weeks, but anyone who doesn't think there's a difference should look at the before and after stats in this league."
In 1984, the last year of the aluminum bat in the Cape Cod League, the league batting average was .273 and the ERA 4.86. Games averaged 11.74 runs scored and 2.08 homers. Last summer's figures: batting average .252, ERA 3.68, runs scored 8.98, homers 0.8 (chart, page 23).
When hitting is altered, pitching is sure to follow, and the aluminum bat has dramatically affected the styles of the pitchers who face it. "Because of aluminum bats, pitching has become an outside game," says Toronto scout Tim Wilken. "Pitchers don't want to pitch inside because, even if they jam a batter [using an aluminum bat], he can dump it to the opposite field for a hit."
"I try to get my pitchers to work inside and forget the opposite-field, jamshot singles," says Long Beach State coach Dave Snow. "But it's tough to get them to do it." Says A's righthander Mike Moore, who was the first pick in the 1981 draft out of Oral Roberts, "It took me years to learn to pitch inside."
"Hitters get conditioned to diving out over the plate to hit the ball," says Wilken. "And because the majority of players in the big leagues today have grown up with that outside style, you see so many hitters get hit or nearly hit by pitches that are very close to being strikes. When major league pitchers use the inside part of the plate, a lot of hitters collapse on the ground as if Bob Gibson had just thrown at them."
Boston righthander Mike Boddicker says, "The strike zone has been pushed out so that the majority of umpires won't call strikes on the inner few inches of the plate. It's practically impossible to get a strike on the inside corner today."
Even more disturbing to some: The aluminum bat practically demands that a pitcher throw breaking balls. "With the aluminum bat the idea is to make the hitter swing and miss," says Grieve. As a result, many in professional baseball believe that college coaches frequently force their pitchers to throw too much breaking stuff.
Says New York Mets vice-president Joe McIlvaine, "When you get 19- and 20-year-old kids throwing a ton of breaking balls, not only do they often hurt their arms, but they don't build up their arms, and therefore their fastballs, at a time when they are developing physically. I cringe when I see some of these college games and coaches are calling 50 and 60 percent breaking balls. The aluminum bat has done a lot of damage to the game, both to hitters and pitchers."
At last month's College World Series, in Omaha, 98% of the bats used were made by the Easton Company of Los Angeles, a firm that went from manufacturing archery products to becoming the largest producer of aluminum bats in America. Easton makes no wood bats, so, not surprisingly, Jim Easton, the company's president and a son of its founder, downplays the differences between wood and metal. "There's more myth than fact to the complaints about the aluminum bat," he says.
Easton cites a 1976 Stanford study that shows that aluminum bats do not drive a baseball farther than wooden bats do, another claim sometimes made about aluminum, and that more variation can be found among baseballs from the same box than between the two kinds of bats. However, the Stanford study was done before advances in aluminum-bat technology began to soup up the bats. "In the late '70s, guys in college all knew that the bats suddenly got livelier," says the Mariners' Bradley.
"Technology changed radically at that time," says Hillerich. "There's a lot you can do with aluminum, and we all learned to do it. The kids wanted it. We offered wood bats free to one local league, and the league was enthusiastic about accepting them. After a few games, the kids all wanted to go back to the aluminum."
"The aluminum process has come so far that we can do anything we want with a bat," says H & B engineer David Ottman. "The colleges want the liveliest, most souped-up bats we can make, and you can't blame the kids for wanting an edge. But we can make an aluminum bat that performs almost exactly like a wood bat. We can make the sweet spot any size we want. We can make the balance points any place we want. We can make it so the weight is the same and the ball jumps the same. The only difference might be in the handle, but we can make it more like a wood action down there than it is now. It just won't break. If the pros sit down with Easton or with us, we can design specifications to fit any of their needs. The bat companies aren't going to stay in the wood business much longer, so baseball might as well start thinking about it."
Easton, H & B and Worth have all experimented with a ceramic-graphite composition bat, which produces a sound more like that of wood and—except near the handle—performs more like wood than aluminum does. "The problem is that those bats involve two elements and they don't hold up to constant usage," says Ottman, whose company does not make such bats. "They're not cost-efficient, and I can't see the day when they'll be perfected. Take batting practice for a couple of hours with one, and it's not the same. The graphite bat is really just to please those concerned with the aesthetics of how they sound."
Says Easton, whose firm does manufacture a graphite composition bat, "A composition bat won't yet outperform aluminum, but it has the potential to be a lot better. Our tests show that our composition bat holds up very well. Graphite is an option, not a replacement for wood."
Such debates will only grow more heated as non-wood bats creep closer to the big leagues. For example, if aluminum bats are more potent, are pitchers endangered by shots back through the box? "If some of these major leaguers used aluminum, someone would get killed," says California Angel hitting instructor Deron Johnson. Easton spokesman Jim Darby counters by saying. "Incaviglia, Cory Snyder and all those guys used aluminum bats in college, and no one got killed."
What about a metallic assault on the game's sacred record books? "If aluminum gets to the majors," says Boston's Wade Boggs. "I'm certain there will be another .400 hitter." Says Easton, "Baseball is obsessed with records, and pro baseball people keep telling us that with the aluminum bat all records would be ruined. But what about the way records are changed by the differences in ballparks? How can you compare records of someone playing in Fenway Park and the Astrodome?"
Finally, will aluminum breed a new generation of artificial hitters, juiced up by a sweeter sweet spot? The Dodgers' Hines believes, to the contrary, that the aluminum bat has made for better hitters. "The first thing in hitting is having the confidence that you can hit," he says. "The aluminum bat gives you that. Kids now don't grow up with the fear of hurting their hands. It's made a tremendous difference, especially to kids living in the north. With a wooden bat, it's nearly impossible to hit on cold days until mid-May, and by then most college and high school seasons are over. With an aluminum bat, you can hit no matter what the temperature. Between the cost factor and the weather factor, aluminum bats are allowing a lot more kids to play. Isn't that good for the game?"
Ping. Get used to it.
[originallink:10661851:702390]
PHOTO
LANE STEWART
The handcrafting of wood bats to meet major leaguers' specs is "financially obsolete."
PHOTO
CRAIG MOLENHOUSE
The aluminum bat initially rocketed in popularity for one simple reason: It won't break.
PHOTO
ANTHONY NESTE
Little Leaguers of today, brought up on aluminum, may know only the ping of the bat.
PHOTO
ANTHONY NESTE
In recent years the College World Series has become exclusively a heavy metal show.
TWO PHOTOS
ANTHONY NESTE
Learning to hit with wood in the Cape Cod League: Juday (left) swings at tennis balls and Kevin Dattola swings in frustration.
PHOTO
NATIONAL BASEBALL LIBRARY
Boning the bat, DiMaggio-style, will soon become the stuff of lore. Say it ain't so, Joe.
CHART
NIGEL HOLMES
ALUMINUM
4"-5"
WOOD
2"-3"
CHART
NIGEL HOLMES
PHOTO
BABE RUTH BY AP; BAT BY DANIEL WAGNER
TWO ILLUSTRATIONS
HOW SWEET IT IS
The sweet spot (deepest purple) is technically a single point, and studies show that a ball struck by a big league—quality wood bat in that spot will go farther than one struck by an aluminum bat in the corresponding spot. But an aluminum bat has a larger area of high performance (dimensions in white circle). It also weighs less than a wood bat of the same length, so a hitter can generate more bat speed. A four-ounce reduction means a batter can eye a pitch for five more feet before swinging.