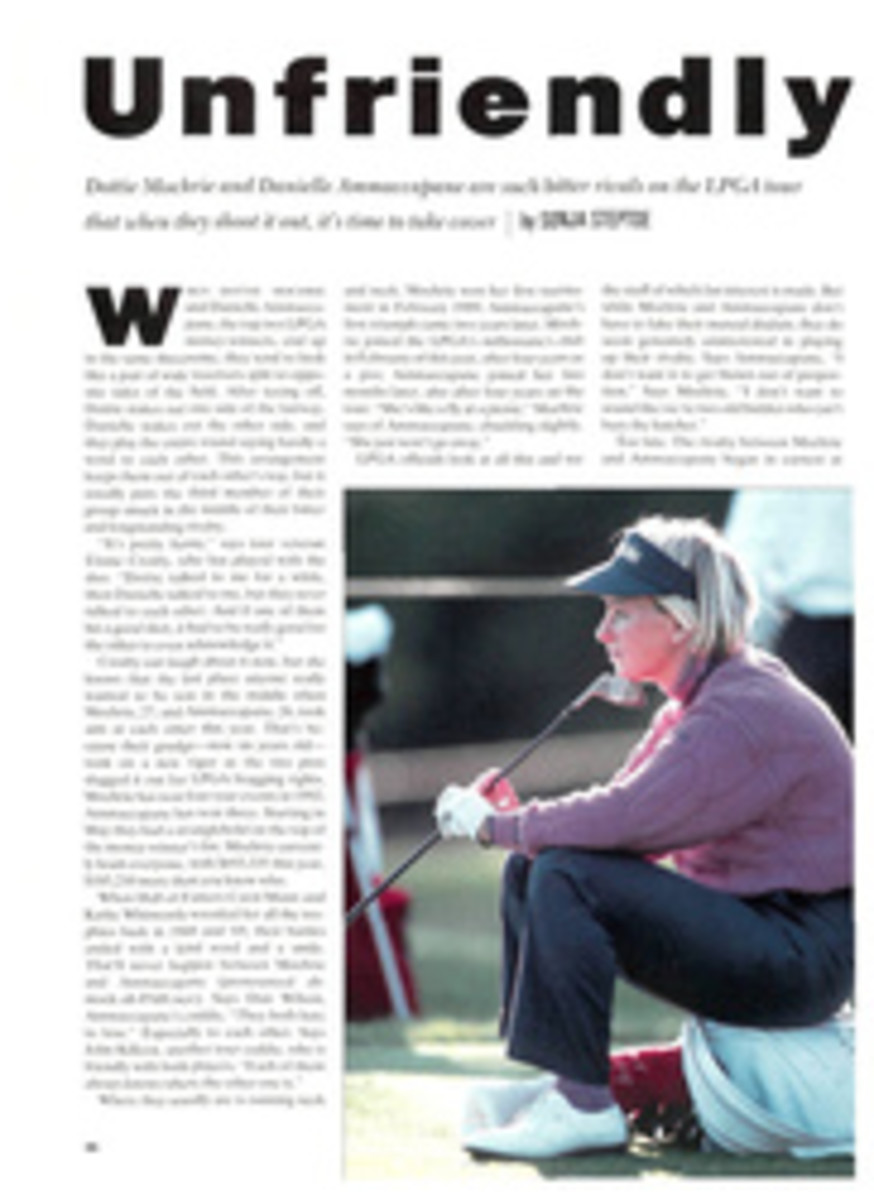
Is It Live or Is It Larson?
Walk in the door of an enormous warehouse in Tucson and you can't miss Marilyn Monroe's right leg lying on the floor. Of course the leg is a fake, but it looks damn good. Nearby, an artist is painting black dots on the nose of a harbor seal made of fiberglass and epoxy.
Continue through the warehouse and you might come across a steel-foam-and-plastic palm tree and hunks of ocean coral made of hard-cast urethane plastic. And in a yard behind the warehouse you'll find a model of Cambodia's magnificent Angkor Wat temple, its imitation-stone visage looking especially grim under Arizona's scorching sun.
This unusual enterprise, situated on 20 acres of desert, is The Larson Company, a big name in the manufacture of artificial environments for zoos, aquariums and theme parks around the world. And don't let a movie star's finely sculpted gam lead you to believe that Larson's work is just frivolous illusion. Some of the company's replicas serve serious environmental purposes.
In fact, what better way to teach people about endangered habitats, such as coral reefs, than to build lifelike copies for the education and enjoyment of millions? For one of the world's largest aquariums, in Osaka, Japan, Larson built a replica of Australia's Great Barrier Reef that includes more than 1,200 pieces of artificial coral, each shaped and colored like the genuine article. Throughout the world's oceans, reefs are dying from a variety of causes, including pollution, damage from ship and boat anchors, and theft by environmental pirates, who pick reefs clean of live coral to sell to gift shops and to the home-aquarium market.
Rain forests, which, according to estimates, are shrinking by 100 acres a minute, are another threatened environment re-created by Larson. The company just finished installing a two-story replica of a rain forest at the Cleveland Metro Parks Zoo, and last year created a 60,000-square-foot rain forest exhibit for Omaha's Henry Doorly Zoo, featuring trees 80 feet tall.
Dave Taplin, Larson's vice-president of construction, says of the company's role as an environmental educator: "A guy who's been living on a corn farm for 45 years can come to the rain forest exhibit in Omaha and sec what we're losing. Maybe that will get him to open his wallet." He adds that a beautiful exhibit is likely to draw the kind of people who are interested in helping to preserve endangered environments.
The Bronx Zoo's Jungle World exhibit, a Larson-built Asian rain forest that's nearly an acre in size, has attracted 3½ million people since it opened in 1985. Says Jim Doherty, curator at the zoo, "We have smaller exhibits within the building that tell of all the medicines and foods and other items that come from tropical rain forests and how none of these will be available if there are no rain forests. By the time people leave here, the message has hit home."
The more lifelike the exhibit, the greater the impact on its viewers, and that is Larson's calling card—creating replicas that are as real as possible. But reproducing nature is an exacting process.
Building an artificial rock, for instance, may require a trip to a distant locale. Although Arizona is rich ground for many varieties and formations of rock, customers sometimes request rocks unavailable in the state. A few years ago, Larson's people traveled to Oregon to obtain molds of a variety of coastal granite that are now featured in an exhibit at the Oregon Coast Aquarium in Newport, Ore.
"We'll travel from Alaska to Costa Rica to make a mold of a specific rock," says company president Harold A. Shifman. "It's like a safari. Our people show up with our equipment and camp out."
Making a rock mold usually requires a three- or four-person crew and 50 to 80 gallons of liquid latex, which is brushed onto the rock in layers, between layers of cheesecloth. Each layer is allowed to cure before being covered with the cheesecloth. Then a "jacket" of poly-urethane foam is sprayed on to make sure the latex holds its shape. Seven days later, when the latex covering is dry, workers peel it off, producing a mold with the exact contours of the rock. Taplin says it takes about 10 days to make 15 to 20 molds, each of which can yield 200 rocks.
To create a banyan tree for a rain forest exhibit, workers begin with a 20- to 40-foot-long column of steel mesh, over which they spread a yellow epoxy mixture that resembles cookie dough. Then an artist painstakingly etches into the epoxy a network of cracks and scratches that mirror those in the banyon tree photographs posted on a nearby bulletin board. A second artist presses a textured pad of rubber against the mixture, and when he pulls it away, the epoxy has the feel of real bark.
The best proof of the replicas' authenticity comes from the animals who live among them. At Tucson's Arizona-Sonora Desert Museum, margays, rare spotted cats from Central and South America, roam over the elaborate Larson-made rock habitat as if it were home. At the Bronx Zoo's Jungle World, gibbons swing on Larson's rubber vines and crawl over its steel and epoxy trees as though the vegetation were the real thing.
Because contented animals are better breeders, well-crafted habitats may help save some species from extinction. The only group of proboscis monkeys in captivity in the Western Hemisphere live in a Larson environment at Jungle World. They flourish there, as do tapir, langurs and gibbons.
"Proboscis monkeys are especially difficult to keep in captivity," says Doherty, "but we have a lot of space, we feed them a good diet and they're breeding very well. A good exhibit is part of what keeps the animals content."
Donald Kuenzer, senior curator at the Cleveland Metro Parks Zoo, believes visitors also benefit from such exhibits. "Nobody wants to see an animal sitting on a concrete shelf in a cage," he says. "People want to see natural-looking things."
Pleasing visitors has a larger value. As Dick George, spokesman for The Phoenix Zoo, says, "If visitors can look at animals in an environment reminiscent of nature, in which the animals are active and enjoying life, they leave thinking the animals are wonderful creatures. They have a heightened sense of respect, which helps the conservation effort."
One of Larson's newer fakes, a saguaro cactus, might ease a problem closer to home. Recently cactus rustlers in Arizona and California have been digging up the giant desert plants and selling them for thousands of dollars on the black market. If enough homeowners and commercial developers begin using replicas of Arizona's signature plant in their landscaping, the rustlers' market could shrink considerably. Larson's saguaro is made from a length of PVC pipe wrapped in foam and covered with fiberglass. It comes complete with a bird hole, fabric and urethane flowers, and cactus needles that are made of bristles from a push broom.
It is fitting that Larson has branched off into saguaros because the company traces its roots to the Sonoran Desert. The company's founder, Merv Larson, was a curator at the Desert Museum, where many of the early habitats he designed are still in use. He left the museum in 1976, and with Taplin helping him, began manufacturing replicas on his own. Five years ago Larson sold his interest in the company—which has 250 employees—to a group of investors.
Part of the company's growth is a result of good timing. As more laws protecting natural habitats have been enacted, the demand by zoos and aquariums for imitation products of nature has risen, especially in the case of coral.
"It used to be that the only way aquariums could get coral was by taking the real stuff," says Dave Powell, director of husbandry at California's Monterey Bay Aquarium. "Because of tighter controls and concerns about taking live coral, aquariums mostly use imitations now."
At Cabela's, an outdoor-equipment supplier in Sidney, Neb., Larson employees recently completed a 25-foot-high, 2,000-square-foot rock mountain built inside the store. Its peak is covered with ice and snow, and distinct climate changes are evident at different points on the mountain—from snow to spruce and aspen to grasslands at the bottom, where there's a stream formed by the melting snow.
"We'll try to make anything," says Taplin. "If someone wants us to build a spaceship 900 feet wide, we'll give it a try."
Oh, yes, in case you were wondering: Marilyn's legs, both right and left, are in a trendy New York City restaurant.
PHOTO
TIM FULLER/SWANSTOCK
Before going to an Ohio aquarium, coral gets a paint job.
PHOTO
TIM FULLER/SWANSTOCK
A single rock mold, which takes about 10 days to complete, may yield 200 replicas.
PHOTO
MANNY MILLAN
Larson environs foster monkey business.
Leo Banks, who lives in Tucson, has written a number of stories for Sports Illustrated.