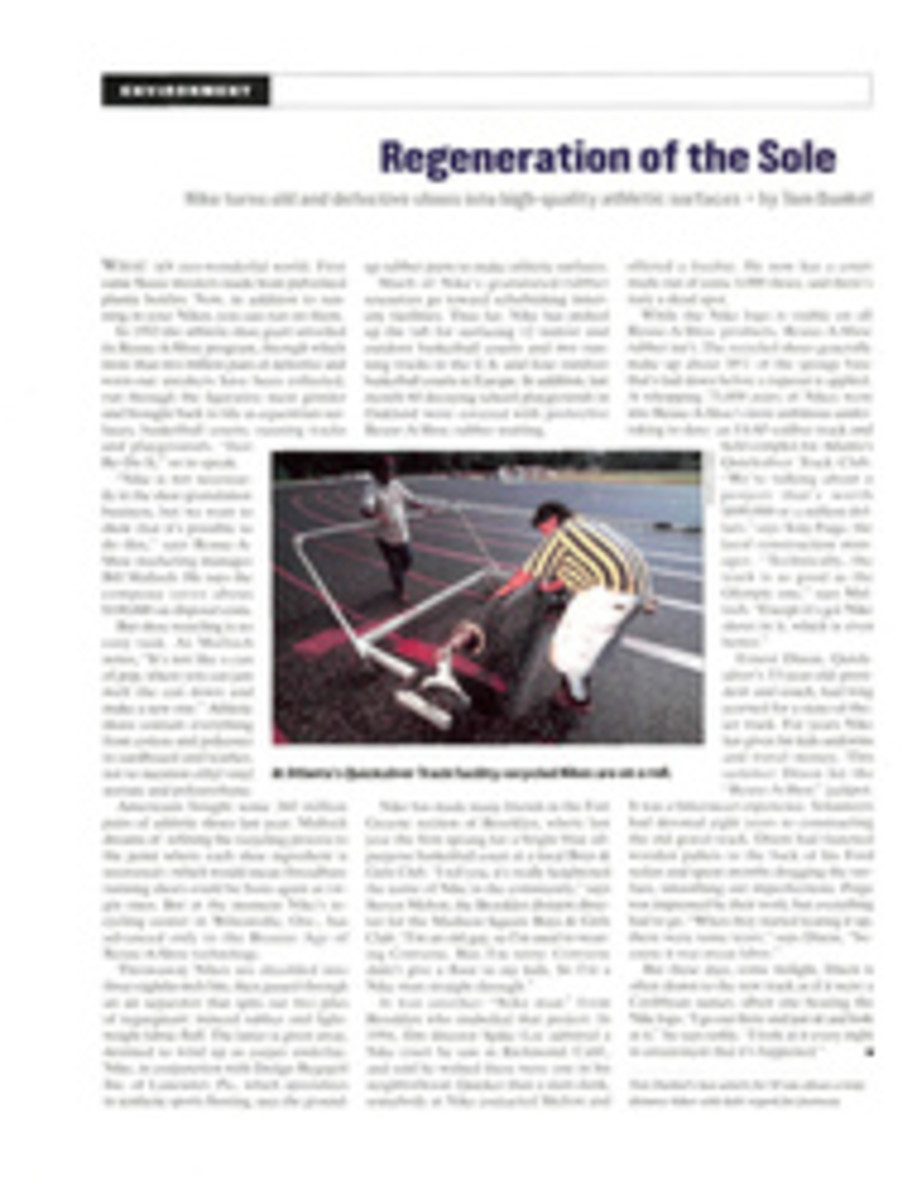
REGENERATION OF THE SOLE NIKE TURNS OLD AND DEFECTIVE SHOES INTO HIGH-QUALITY ATHLETIC SURFACES
What an eco-wonderful world. First came fleece sweaters made
from pulverized plastic bottles. Now, in addition to running in
your Nikes, you can run on them.
In 1993 the athletic shoe giant unveiled its Reuse-A-Shoe
program, through which more than two million pairs of defective
and worn-out sneakers have been collected, run through the
figurative meat grinder and brought back to life as equestrian
surfaces, basketball courts, running tracks and playgrounds.
"Just Re-Do It," so to speak.
"Nike is not necessarily in the shoe-granulation business, but
we want to show that it's possible to do this," says
Reuse-A-Shoe marketing manager Bill Malloch. He says the company
saves about $100,000 on disposal costs.
But shoe recycling is no easy task. As Malloch notes, "It's not
like a can of pop, where you can just melt the can down and make
a new one." Athletic shoes contain everything from cotton and
polyester to cardboard and leather, not to mention ethyl vinyl
acetate and polyurethane.
Americans bought some 360 million pairs of athletic shoes last
year. Malloch dreams of refining the recycling process to the
point where each shoe ingredient is recovered--which would mean
threadbare running shoes could be born again as virgin ones. But
at the moment Nike's recycling center in Wilsonville, Ore., has
advanced only to the Bronze Age of Reuse-A-Shoe technology.
Throwaway Nikes are shredded into three-eighths-inch bits, then
passed through an air separator that spits out two piles of
regurgitant: minced rubber and lightweight fabric fluff. The
latter is given away, destined to wind up as carpet underlay.
Nike, in conjunction with Dodge-Regupol Inc. of Lancaster, Pa.,
which specializes in synthetic sports flooring, uses the
ground-up rubber parts to make athletic surfaces.
Much of Nike's granulated-rubber resources go toward
refurbishing inner-city facilities. Thus far, Nike has picked up
the tab for surfacing 12 indoor and outdoor basketball courts
and two running tracks in the U.S. and four outdoor basketball
courts in Europe. In addition, last month 60 decaying school
playgrounds in Oakland were covered with protective Reuse-A-Shoe
rubber matting.
Nike has made many friends in the Fort Greene section of
Brooklyn, where last year the firm sprang for a bright blue
all-purpose basketball court at a local Boys & Girls Club. "I
tell you, it's really heightened the name of Nike in the
community," says Steven Melton, the Brooklyn division director
for the Madison Square Boys & Girls Club. "I'm an old guy, so
I'm used to wearing Converse. But, I'm sorry: Converse didn't
give a floor to my kids. So I'm a Nike man straight through."
It was another "Nike man" from Brooklyn who midwifed that
project. In 1994, film director Spike Lee admired a Nike court
he saw in Richmond, Calif., and said he wished there were one in
his neighborhood. Quicker than a slam dunk, somebody at Nike
contacted Melton and offered a freebie. He now has a court made
out of some 4,000 shoes, and there's nary a dead spot.
While the Nike logo is visible on all Reuse-A-Shoe products,
Reuse-A-Shoe rubber isn't. The recycled shoes generally make up
about 30% of the spongy base that's laid down before a topcoat
is applied. A whopping 75,000 pairs of Nikes went into
Reuse-A-Shoe's most ambitious undertaking to date: an
IAAF-caliber track and field complex for Atlanta's Quicksilver
Track Club. "We're talking about a project that's worth $800,000
or a million dollars," says Tony Paige, the local construction
manager. "Technically, the track is as good as the Olympic one,"
says Malloch. "Except it's got Nike shoes in it, which is even
better."
Ernest Dixon, Quicksilver's 53-year-old president and coach, had
long yearned for a state-of-the-art track. For years Nike has
given his kids uniforms and travel money. This summer Dixon hit
the "Reuse-A-Shoe" jackpot. It was a bittersweet experience.
Volunteers had devoted eight years to constructing the old
gravel track. Dixon had fastened wooden pallets to the back of
his Ford sedan and spent months dragging the surface, smoothing
out imperfections. Paige was impressed by their work, but
everything had to go. "When they started tearing it up, there
were some tears," says Dixon, "because it was sweat labor."
But these days, come twilight, Dixon is often drawn to the new
track as if it were a Caribbean sunset, albeit one bearing the
Nike logo. "I go out there and just sit and look at it," he says
softly. "I look at it every night in amazement that it's
happened."
Tom Dunkel's last article for SI was about a long-distance hiker
with little regard for footwear.
COLOR PHOTO: GREG FOSTER At Atlanta's Quicksilver Track Facility recycled Nikes are on a roll. [Men unrolling new surface for track]